When it comes to designing, developing and testing a vehicle, perhaps the most important components to affect its overall performance are the tires. They contribute to the stiff and sharp behavior of a sportscar, the rumble-absorbing capability of an SUV and the overall ride and handling of every vehicle. Although they contact the road in just four hand-size patches, tires generate the primary forces that cause the vehicle to move in response to all driver controls.
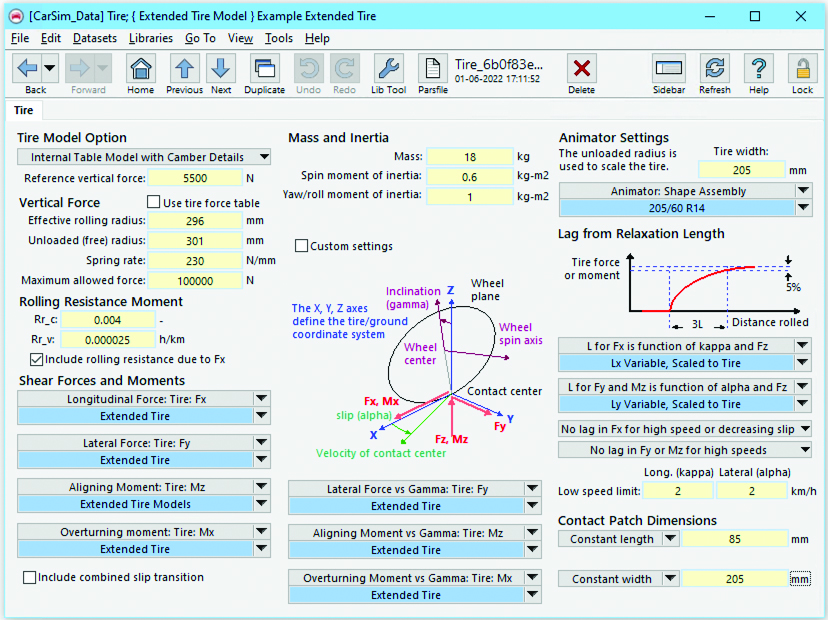
When close matching of simulation and test results is required, detailed measurements of the specific model of the tires can provide data that can closely reproduce the behavior of the vehicle over a full range of operation. On the other hand, when simulations are used for evaluating controllers in ADAS and/or autonomous vehicle behavior over a wide range of conditions, it is often acceptable to have tire data in the simulation model that might not match a specific test vehicle but is generally representative of a tire that could exist. The CarSim software tools from Mechanical Simulation Corporation (and the similar tools, TruckSim and BikeSim) include tire options that cover a range of requirements for various types of simulated testing.
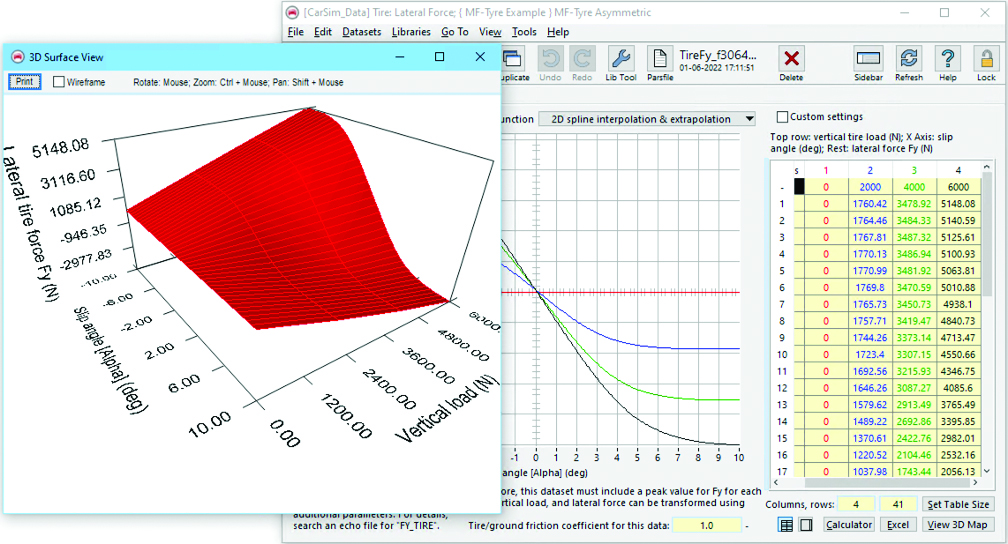
The tire models operate by using the instant kinematics of the non-linear 3D multibody vehicle model to determine the relationship between the tire and ground in the contact area in terms of instant tire radius, inclination angle, slip angle for steering and longitudinal slip for braking and acceleration. The tire model obtains information about the ground properties from one or more points, with the properties of interest being the elevation, possibly the 3D slope (if a single point of contact is used), a component of the tire/ground friction and a component of the tire rolling resistance on the surface.The built-in CarSim tire model supports the full non-linear behavior of rolling tires subject to combined braking/acceleration and cornering on roads with variable friction and rolling resistance. The models have dynamic responses due to lateral and longitudinal relaxation length that are functions of load and slip. The tire models handle the transition to zero speed to properly simulate parking lot maneuvers and driving simulator conditions. There are several options to simplify the required data: the forces and moments can be assumed to be symmetric to reduce the details in the data, and they can use a simplified representation of camber effect when non-linear data is not available.
CarSim supports a tiered approach for most data, including tires: simple, extended and external. The built-in extended tire model covers a full range of conditions, for any feasible geometry relative to the ground surface, and using combined slip and friction ‘similarity’ to cover a full range of friction and slip. However, if the full range of conditions is not covered in the data, the model will make good use of more limited data (assumed symmetry, limited interactions between steer and camber).
CarSim also supports external tire models using the VS (VehicleSim) standard tire interface (STI) that provides built-in support for external commercial tire models from Siemens (MF-Tyre and MF-Swift), Cosin (FTire) and Michelin (TameTire). The VS STI includes C source code and documentation for connecting with arbitrary external tire models. This interface also supports custom in-house tire models for some of the OEM users of CarSim. The built-in tire models also work on real-time (RT) hardware-in-the-loop systems.
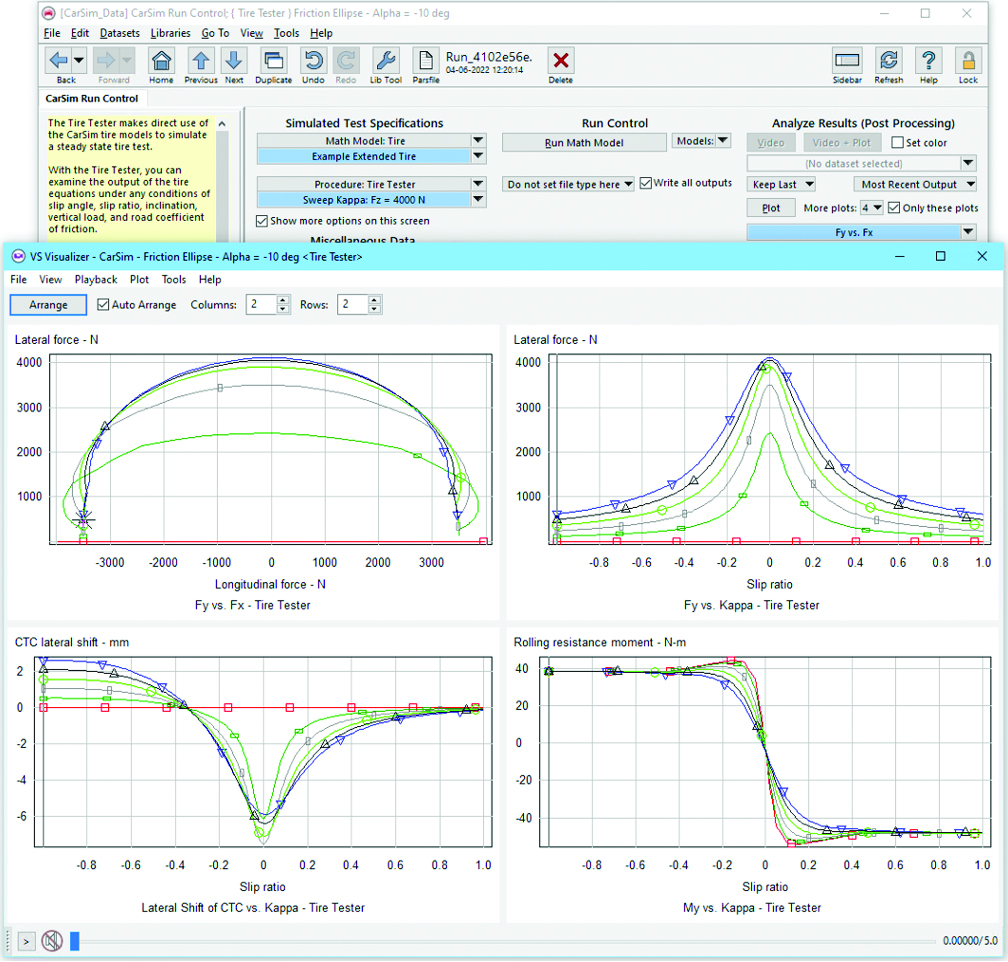
Most external commercial tire models are also available for the major RT platforms. Another option favored by some advanced users involves modifying the tire model behavior using built-in scripting (no external software) with VS commands. Custom external model extensions can be used with MATLAB, Python, Visual Basic and ANSI C languages. To help users validate their settings in the various tire models, CarSim includes a built-in tire tester tool for users to confirm that the tire data produces the expected behavior in the controlled setting of a tire assessment.
The tire parameters and tables can be obtained from published data, engineering tools and test rigs. When data is not available, users can use the real-world data provided in Mechanical Simulation’s sample data sets.
CarSim’s modular, parameter-based design approach enables engineers to modify parameters and run simulations any time during the design cycle. “With more than 25 years of real-world validation by engineers, CarSim is universally the trusted tool for analyzing vehicle dynamics, developing controllers, calculating a car’s performance characteristics and engineering next-generation active safety and AV systems,” says Mike Sayers, Mechanical Simulation’s CTO.
Tires play a key role in capturing reliable simulation results. For an engineer to be able to deliver on tight timelines, it is critical that they can rely on their simulation results. CarSim provides an intuitive set of tools to quickly evaluate decisions with a model that ensures the simulation can be trusted to represent the vehicle’s performance in the real world.