2024 will see a bumper crop of entries in the Hypercar category
at Le Mans, with a total of nine manufacturers contributing 22 cars to the
grid. This year’s race will be mark the debut of three new LMDh cars, from
Lamborghini, BMW and Alpine (though in the case of BMW, it has completed a year
running in IMSA), while Isotta Fraschini joins the ranks of LMH with the Tipo 6
LMH-C.
Le Mans BoP table for Hypercar
Le Mans 2024 pitlane tech highlights
Why is BoP necessary when technical regulations dictate the
performance window of a car? PMW investigates where pace can be won and
lost in the Le Mans Hypercar class.
The centenary edition of the 24 Hours of Le Mans proved to be one of
the most emotional and exciting races in many years. The competition for
the win was intense, with numerous cars displaying potential winning
pace. Different teams led at various stages of the competition, creating
a thrilling battle throughout. The typical Le Mans weather added drama
and tension, making race engineers’ jobs even more complex. The ultimate
fight for victory came down to Ferrari and Toyota, who battled fiercely
until the last hour.
Meanwhile, off the track, last-minute changes to the balance of
performance (BoP) in the Hypercar class caused no small controversy in
the paddock. The need for a BoP system (see Class wars, page 39) in a
class where the cars should be matched by regulation is justified by the
many parameters that cannot easily be given targets. This feature will
look to understand the performance sensitivity of these parameters at Le
Mans, and assess their impact on lap time.
Meanwhile, off the track,
last-minute changes to the balance of performance (BoP) in the Hypercar
class caused no small controversy in the paddock.
For example, mass distribution front to rear is used to tune car
behavior, and the center of gravity height is also critical for race
cars. The regulations mandate the height of the center of mass of some
key components, so there are no huge differences between different
manufacturers, but each car still has some variation.
Suspension design and kinematics is another important differentiator
and can play a significant role in terms of performance. This includes
suspension systems compliance, which, together with kinematics, defines
how the wheels are placed dynamically with respect to the road and
influences how the tires are exploited.
Even in respect to the aerodynamics and powertrain power, which the
regulations define so strictly, there can be differences that are worth
significant pace on track, even though the cars still fulfill the
homologation criteria.
Performance constraints
For powertrain, the regulations stipulate not only the maximum power for
each engine speed (power curve) but also how the targets can
momentarily overshoot and for how long. In terms of design, the key is
for the teams to stay as close to the power target as possible without
being over it and risking a disqualification. Besides the combustion
engine itself, a key factor is how the teams can control the
instantaneous power at the wheels, balancing the ICE and the electric
motor (if the car is a hybrid). Critical is how much tolerance they need
to build into the system to avoid going over the regulation targets.
This control is closely related to how effective their control systems
and strategy are. It would be nearly impossible to hit the exact power
target all the time, so teams must retain a small safety margin under
this target.
With respect to the
aerodynamics, there are some aspects that could make a difference
between two cars, even if both fulfill the regulations and achieve
homologation
With respect to the aerodynamics, there are some aspects that could
make a difference between two cars, even if both fulfill the regulations
and achieve homologation. The rules dictate how the performance of the
cars (compared with the targets) must be measured and calculated. For
drag, the reference condition is representative of an end-of-straight
scenario in terms of ride height (considered to be the lowest setting);
however, for downforce the definition is more complex and is based on a
weighted average over a wider range of ride heights, roll angles and yaw
angles.
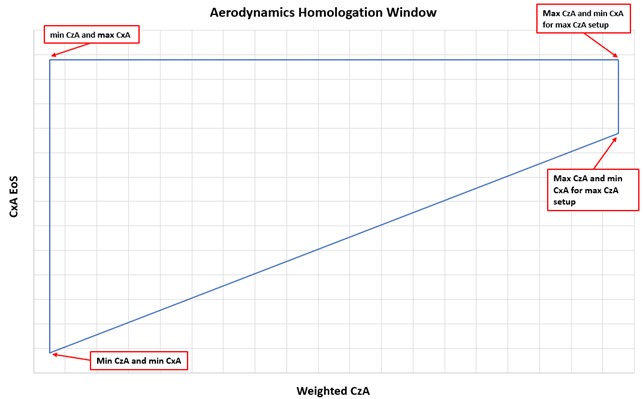
Moreover, in each aerodynamic configuration (this includes any
possible setting of the single adjustable aero device the cars are
permitted to deploy – an adjustable rear wing, for example), the two
target values calculated as above must remain within a given window.
This is shown in Figure 1. Cx and Cz are respectively the drag and
downforce coefficient of the car; they are multiplied by the frontal
area to get to CxA (vertical axis) and CzA (horizontal axis) as shown in
the diagram.
BoP in action
In a scenario without balance of performance regulations, each team’s
objective would be to position itself along the lower diagonal line of
the diagram. This line connects the configurations with minimum and
maximum downforce at the minimum allowed drag. BoP serves to level the
playing field for cars that might perform in less advantageous areas of
the homologation window. For instance, some teams may sacrifice
performance to incorporate styling cues linked to a manufacturer’s road
cars.
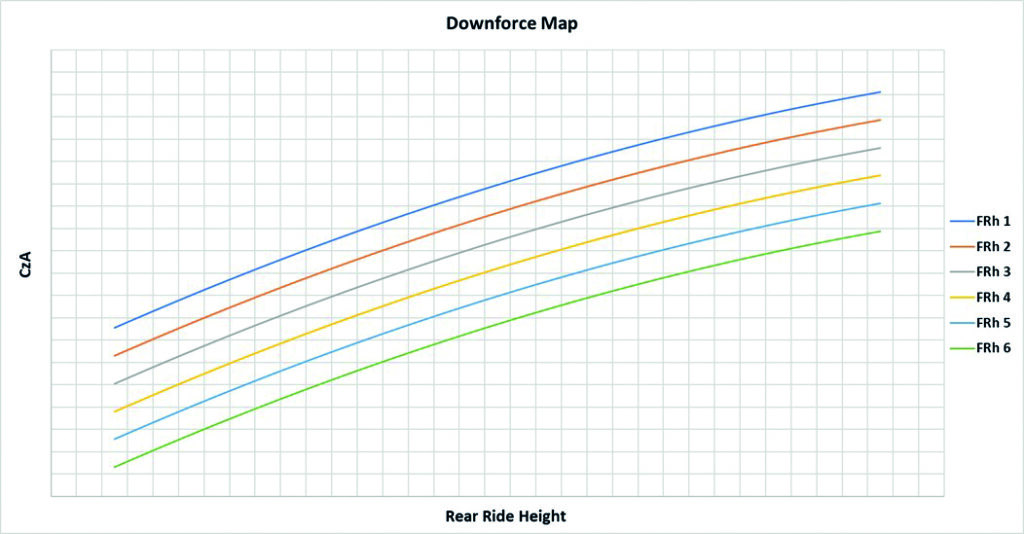
Downforce map used for the base vehicle model. Each curve represents a
specific front ride height. Rear ride height is on the horizontal axis,
downforce (in form of CzA) is displayed on the vertical axis
Furthermore, teams will have invested significant effort in
manipulating the aerodynamic behavior of their cars, specifically how
much downforce and drag are generated at different attitudes, such as
front and rear ride heights, roll and pitch angles.
The effects of these aspects, as well as the adjustments made to the
balance of performance just before the 24 Hours of Le Mans, are
thoroughly analyzed. The adjustments were controversial, not only due to
their favoring the winning Ferrari team but also because the FIA/ACO
had previously assured teams that no BoP adjustments would be made until
after Le Mans.
Methodology
To conduct this analysis, the author used a lap time simulation tool
that he developed and deployed with active sportscar racing teams.
A model of a rear-wheel-driven LMH/LMDh vehicle under qualifying
conditions was created, based on data found within the regulations, in
addition to information gathered by the author, including insights from
engineers working in various WEC teams. Vehicle mass and maximum power
values were those assigned to Cadillac for Le Mans. The LMH tires were
modeled based on data from LMP2 rubber, with adjustments made to account
for the different dimensions used in Hypercar. Suspension kinematics
and compliance were based on those of real Le Mans prototypes, providing
a reasonable representation of an LMH vehicle. Regarding aerodynamics,
aero
maps were generated by fitting a mathematical model to a car with
similar characteristics, sensitivities and performance to those that
LMH/LMDh teams are targeting. These mathematical models were then
manipulated to investigate how different sensitivities would influence
the cars’ performance while still adhering to the regulations.
The track model used in the simulations was constructed from logged
data acquired at Le Mans, taking elevation changes into account.Lap time
simulation results come with caveats and it is worth bearing two key
points in mind:
- Since the vehicle model is not based on detailed data of a specific
car, and due to the nature of simulations themselves, the results should
notbe looked at in terms of absolute performance, rather to identify
trends following specific changes to vehicle properties. Furthermore, it
must be remembered that the accuracy of the track model can be crucial
to the final simulation results.
- The results should be considered as something like an upper
envelope, both in terms of absolute performance and its relative
changes.
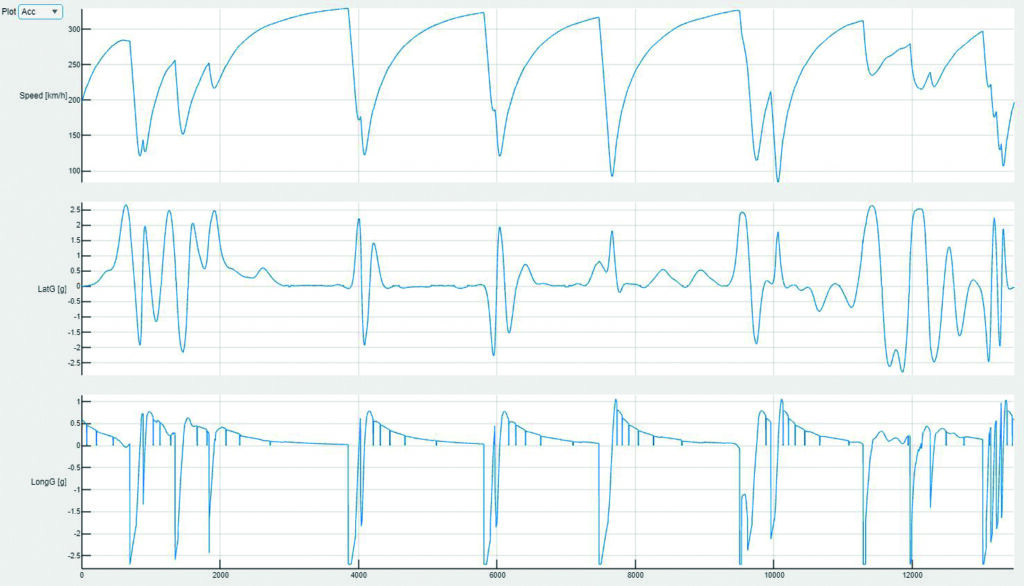
A simulated lap of Le Mans with the reference configuration. The top
trace shows vehicle speed, lateral acceleration is in the middle and
longitudinal acceleration at the bottom
The reference model as set up for the first runs produced a lap time
of 3:22.099 (Figure 3). This is about 0.9 seconds faster than Ferrari’s
pole position, clocked at 3:22.982. In relative terms, the mismatch is
around 0.4%.
The model achieved a top speed of 329.2km/h on the first Hunaudières
straight, while maximum lateral accelerations were achieved in the
Porsche curves, specifically between the 11,000m and 12,450m distance
marks.
Analysis
The initial investigation focused on a simple mass scan, taking into
account the weights assigned to each car by the BoP table for Le Mans.
Figure 4 displays the results in tabular and plotted forms.
The results reveal a sensitivity of about 0.405 seconds for a 10kg
change in vehicle mass. It is apparent that Toyota had to endure a
significant performance penalty of about two seconds to level the
playing field for privateers competing against the fastest cars.
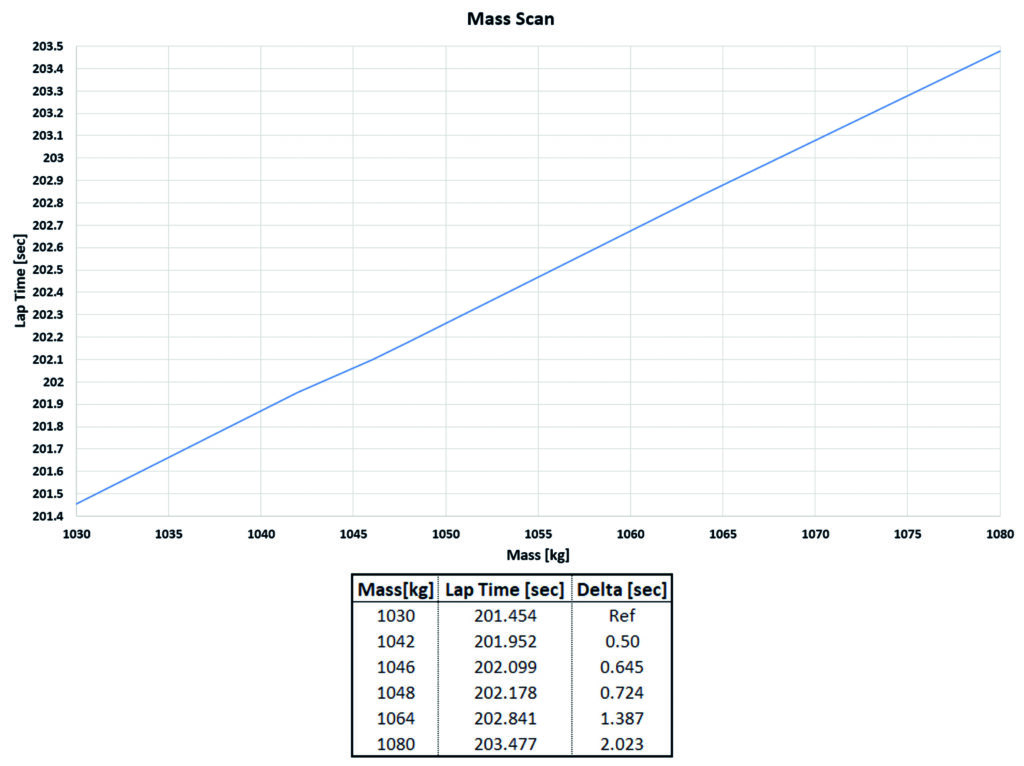
With the late BoP adjustment only changing the mass assigned to some
cars, the next logical step was to quantify the performance change of
each car whose weight was modified between Le Mans and the previous race
in Spa Francorchamps. Figure 5 summarizes these results, with each
adjusted car marked in a different color.
If all cars had started at the same level, the performance difference
between Porsche and Toyota due to the BoP in Le Mans would have been
over 1.6 seconds. In other words, the regulators estimated that LMDh
Porsche needed a boost of 1.6 seconds to be competitive against Toyota.
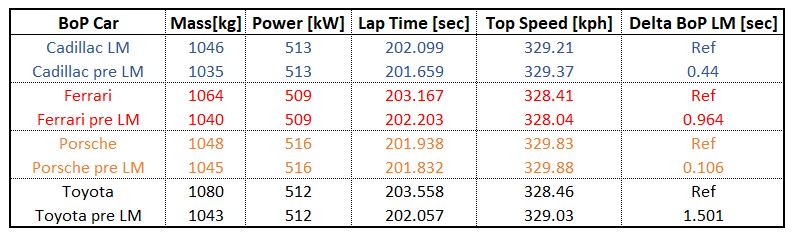
In terms of race results, while Ferrari’s performance was slowed down
by about 0.964 seconds, Toyota’s performance was reduced by 1.5
seconds, meaning over half a second per lap more than Ferrari.
To put this into context, the winning Ferrari car (n.51) produced an
average lap time about 0.42 seconds faster than Toyota car n.8’s fastest
driver. When considering the average of the best 20% green laps,
Ferrari n.51 was ahead of Toyota n.8 by about 0.3 seconds.
Interestingly, the fastest car on track was Ferrari n.50, about 0.6
seconds quicker than the winning sister car and 0.9 seconds faster than
Toyota n.8, based on the average of the best 20% green laps.
Performance nuance
As for whether the BoP adjustment was excessive, that is for the reader
to decide. However, other aspects related to powertrain and aerodynamics
may explain why such significant performance differences between cars
need to be ‘artificially’ corrected by adjusting the BoP.
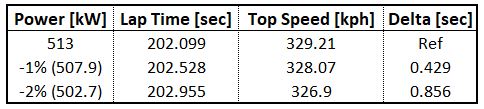
To understand the impact of ensuring that power measured at the
wheels is kept under the regulation limit to avoid disqualification, the
effect on performance can be quantified with a power scan. The results
of a power reduction (or margin) of 1% and 2% are shown in Figure 6.
These values have been chosen as they should provide a realistic
representation of the safety margin teams typically implement.
While a 1% change in engine power may seem small, it results in a lap
time deterioration of over 0.4 seconds at Le Mans. Figure 7 provides a
comparison of lap times between the baseline and the -2% power
configuration.
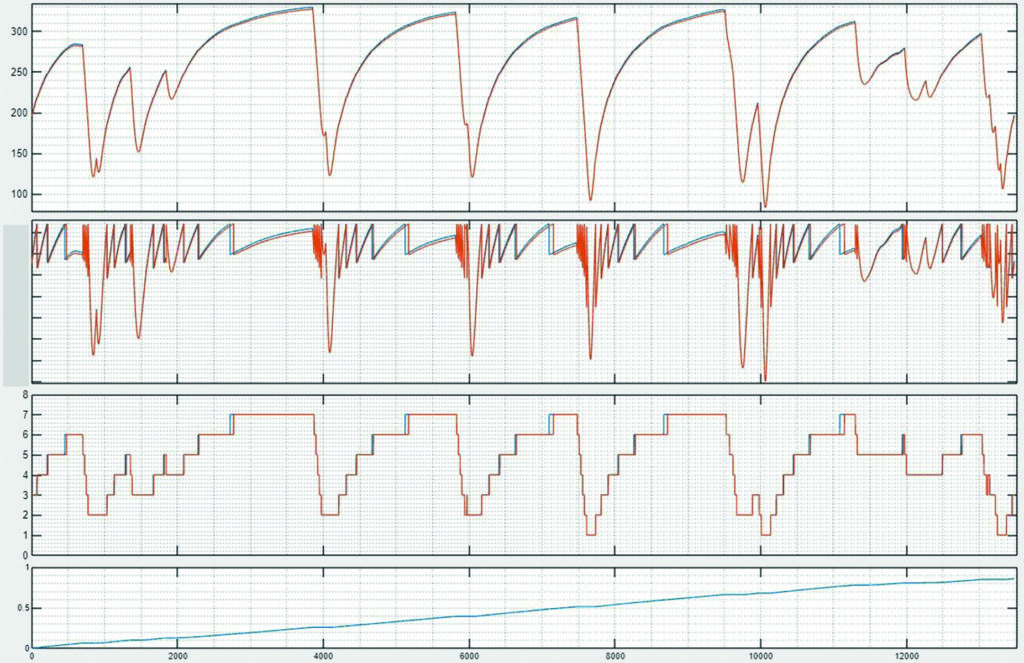
Comparison between the base run (blue) and the one with 2% less power
(orange). From the top, the shown traces are: speed, RPM, engaged gear
and compare time. Plots have traveled distance on the horizontal axis
Now, let’s explore scenarioswhere a car does not fully exploit the
aerodynamic homologation window shown in Figure 1. Two specific
scenarios were investigated: one where the car does not meet the minimum
drag target while remaining at the minimum downforce level (lower
aerodynamic efficiency, depicted on the left edge of the trapezoid in
Figure 1), and another where the car experiences an increase in both
downforce and drag while staying within the efficiency edge allowed by
the rules (lower diagonal of the trapezoid in Figure 1).
The first scenario can be analyzed with a drag scan, and the results
are summarized in tabular and plotted forms in Figure 8. The findings
suggest that balance of performance corrections would be necessary to
compensate for a car that is not optimally designed in terms of
aerodynamic performance. The impact of drag on performance at Le Mans is
considerable, with a 1% increase in drag resulting in approximately
0.19 seconds of lap time and slightly less than 1km/h reduction in top
speed.
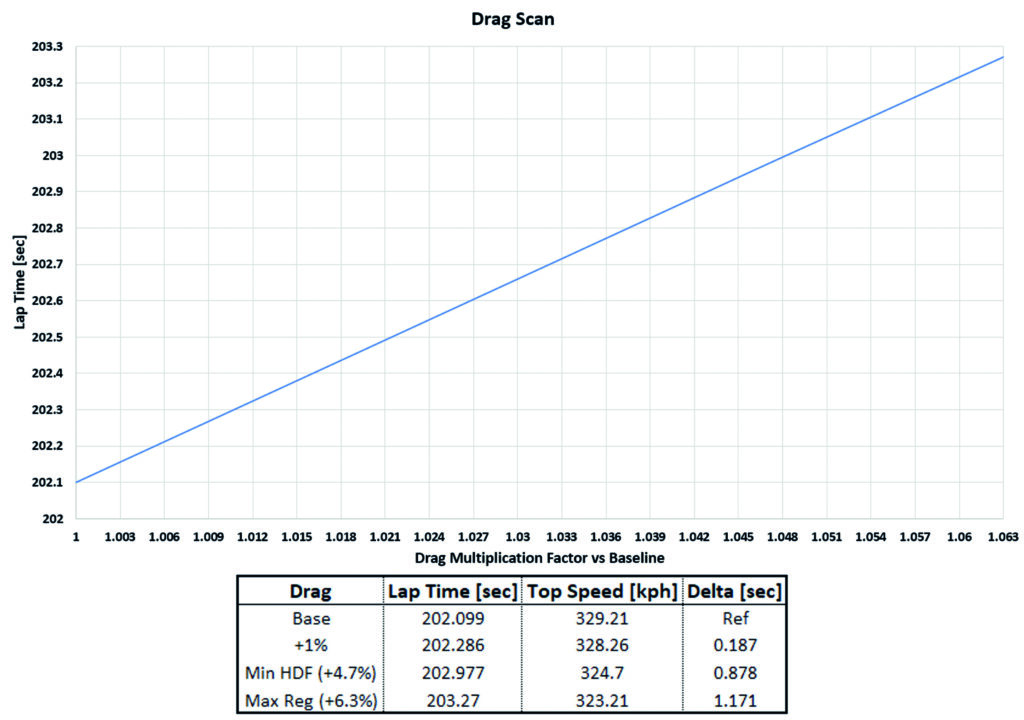
the same
The second scenario was analyzed by proportionately increasing both
drag and downforce (though not by exactly the same amount because of
slight efficiency changes) while maintaining a constant aerodynamic
balance through a reference fast corner. This was achieved by adjusting
the static rear ride height. The results are summarized in Figure 9.
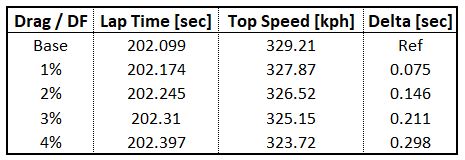
This analysis represents a scenario where a car, either due to design
considerations or setup requirements, operates at the maximum
aerodynamic efficiency allowed by the regulations but does not reach the
lowest permitted level of drag or peak downforce. The increase in
downforce and drag was limited to around 4%, as the rules specified a
maximum difference of 4.5% between minimum and maximum downforce.
Consequently, the difference in lap time between the lowest and highest
downforce/drag setup is approximately 0.3 seconds, with a top speed
reduction of 6.5km/h. Figure 10 provides a comparison between the base
configuration and the highest downforce/drag setup considered in this
analysis.
This gives a compelling visual representation of why drag is crucial
in Le Mans. By comparing the time and speed traces, it becomes evident
that the orange run is faster in each corner, particularly the faster
turns. However, the gains made in corners are overshadowed by the lower
straight-line performance. The second trace clearly indicates higher
downforce for the orange run, while the third highlights the consistent
aerodynamic balance in the faster corners, where it makes the greatest
difference.
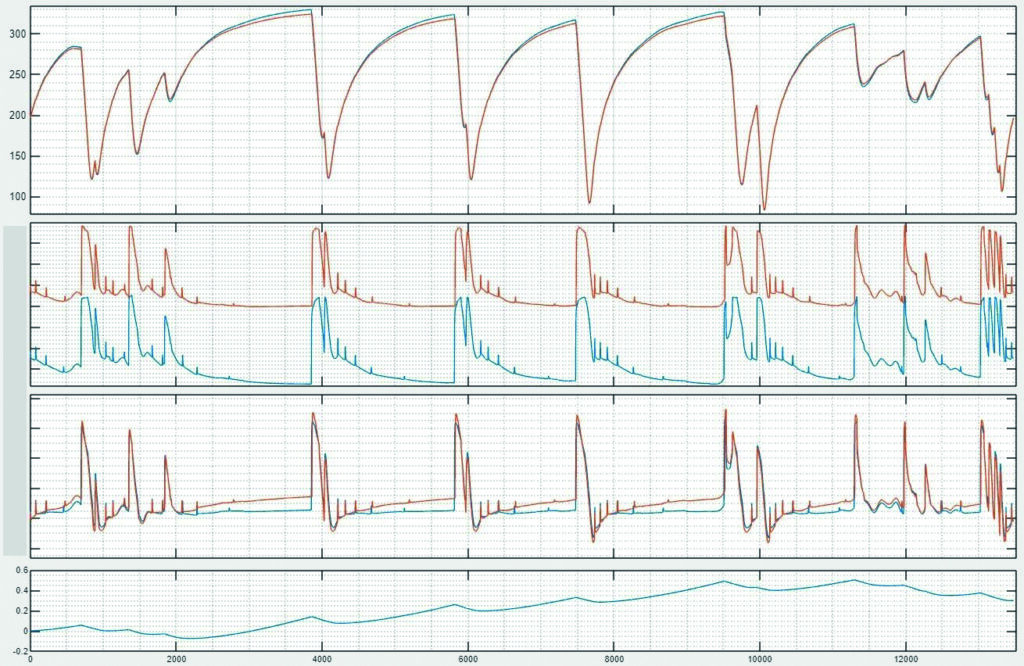
Comparison between the base run (blue) and the one with 4% more
downforce and drag (orange). From the top, the shown traces are: speed,
downforce coefficient (CzA), aerodynamic balance and compare time. Plots
have traveled distance on the horizontal axis
In the final analysis for this article, we delve into a case where
the car, while positioned at the same point (minimum drag and downforce)
within the aerodynamics homologation box, has a different aerodynamic
map from the baseline.
As previously explained, the aero maps were generated using
equations, with coefficients fitted to a car similar to an LMH/LMDh in
terms of key aerodynamic features, and then scaled to meet regulations.
This allowed selective modifications of drag and downforce sensitivity
to ride heights. This process could be used to set performance targets
for a team’s aerodynamics department.
In the first step, the drag sensitivity to rear ride height was
reduced by approximately half. In the second step, downforce sensitivity
to rear ride height was also diminished. The results are summarized in
Figure 11.
As expected at Le Mans, the most significant effect is produced by
varying drag. Reducing drag rear ride height sensitivity results in a
lap time drop of over 0.4 seconds while increasing top speed by about
1.5km/h. This is because the drag homologation target applies to a
specific driving condition, and ideally the car would maintain this
minimum allowed drag across all ride heights.
Interestingly, although reducing downforce sensitivity to rear ride
height has a smaller impact on lap times, it still leads to an
improvement. If designing for lower drag sensitivity to rear ride height
also means lower downforce sensitivity, the advantage becomes clear.
Figure 12 illustrates a comparison between the results of the simulation
for the base setup and the lower downforce and drag sensitivity setup.
The setup with lower rear ride height sensitivity results in lower
drag (better straight-line performance) and higher average downforce
over a lap. In other words, both top speed and corner speed improve.
In conclusion, this article highlights how the current WEC top class,
despite strict regulations limiting vehicle performance in various
ways, still offers significant opportunities for optimization, hence why
it is deemed necessary to implement a BoP system to level the playing
field.
Though purists find this approach disturbing as it artificially
brings cars to a similar performance level, it cannot be denied that it
has led to exciting races and attracted numerous prestigious
manufacturers to the LMH class, not least due to the much lower budget
that is required to compete compared with the relatively open
development of LMP1.
Class wars
The 2023 edition of the 24 Hours of Le Mans brought a thrilling
spectacle thanks to the Le Mans Hypercar (LMH) class featuring multiple
manufacturer and privateer entries. Although the regulations for this
class remained largely unchanged since their implementation in 2021 for
the World Endurance Championship and Le Mans, 2023 saw the arrival of
major players including Ferrari, Porsche, Cadillac and Peugeot,
alongside privateer teams such as Vanwall and Glickenhaus. This
impressive line-up saw a stellar grid of 16 cars in the top class.
One of the reasons for the success of this event was the blending of WEC
technical rules with those of IMSA’s GTP class (for LMDh cars). These
LMDh cars are built on a ‘standard’ LMP2 chassis, which must be provided
by one of four chosen chassis manufacturers: Dallara, Oreca, Ligier and
Multimatic.
Ensuring a balanced performance window for both classes was a crucial
element that allowed LMH and LMDh/GTP cars to compete together. The
regulations were designed to ensure that all cars would deliver similar
performance on the track. This was achieved by setting the target
aerodynamic efficiency (downforce to drag ratio) for LMH/LMDh cars at
least 50% lower than that achieved by LMP1 cars. Additionally, specific
parameters were defined to control downforce and drag figures within a
specified homologation window. To level the playing
field further, the class implemented a BoP system. This allowed
regulators to adjust various parameters, such as the car’s overall mass,
maximum power and energy use during a stint. The intention was to
prevent any team from gaining an advantage and maintain competitive
racing.
Despite the regulations’ efforts to limit key performance drivers,
the need for a BoP adjustment prior to Le Mans, forced through without
the agreement of the teams, arose due to what the ACO and FIA called a
performance differential across the field that was ‘greater than
anticipated’.
The cars
Having soldiered on as the lone manufacturer in LMP1, following the departure of Audi and finally Porsche in 2017, Toyota was the first OEM to sign up to the new balance of performance-based Hypercar rule package when it was announced in 2018. However, getting a head start was not necessarily the advantage it may first seem. As the machinations of rule makers flickered back and forth, early decisions taken on long lead parts could not be easily altered to better suit new rules, and it wasn’t able to fully exploit the finished regulation package.
Following the TS family of LMP1’s almost decade of development, Toyota evidently wanted to maintain the lineage, and at first glance the family similarity between the previous model and the GR010 is clear. The basic architecture of the car carries much over from its forebear: a mid-mounted, 520kW (698bhp), 3.5-liter twin-turbocharged V6 – in 2021 Le Mans trim – sits behind the driver, while a 200kW (268bhp) hybrid motor equips the front axle. The Hypercar rules permit only a single MGU rather than the two allowed in LMP1, and total power output is capped at 520kW. The demands of the rules have subtly altered the car’s proportions compared with the TS line. For example, the tub is longer due to a stipulation that the battery must now be housed behind the driver (the TS050’s was placed in the passenger compartment), and notably the overall vehicle weight is also some 162kg heavier, at 1,040kg.
Chopping and changing
John Litjens, project leader for Hypercar at Toyota Gazoo Racing (TGR), explains that one of the greatest challenges faced while developing the car was adapting to the evolving rule set. “The biggest impact was from the relatively late minimum weight changes,” says Litjens, as initially, the minimum weight for LMH was set at 1,100kg. “When you have a high minimum weight, you want to spend weight for reliability, much more than we did with the LMP1. You design the car to take some ballast, but when you suddenly have the weight reduced by 60kg, that ballast you planned is all gone.” It might be assumed that as TGR was able to build an LMP1 car with two hybrid systems and a large battery down to a weight of 875kg, finding last-minute savings in the LMH would be straightforward.
However, as Litjens points out, the rules set minimum weights for parts such as the tub, engine, gearbox and other systems. “I think if we had known from the start it would be 1,040kg for the hybrid cars, it would have been relatively easy. For example, with the engine, if you think it can be a bit more reliable by going a little over the minimum weight, you take advantage of that because you have the overall weight to spend. If that weight is suddenly not available, but the designs are kicked off on a long lead time item, it is too late to change.” The same consideration applied to providing leeway to ballast the car’s weight distribution, ensuring it could work with what was still an under-development tire from Michelin. “If you have 50-60kg to play with, you can do quite a lot,” muses Litjens. “If you have nothing, then you are stuffed.”
Certain regulation requirements have also contributed to the extra mass, beyond the stipulated minimums. For example, the longer monocoque and battery positioning meant the GR010 inherently incorporates more material than the LMP1 version. Toyota also took advantage of the increased overall weight to make the tub more resilient. “For example, with the suspension mounting points, where in the past we had a certain safety factor built in, we have increased that,” says Litjens. The desire for extra robustness was not solely related to track conditions, but also to the changing nature of the racing Toyota expected to encounter. “With the BoP you will have tighter fights [than in LMP1] and there might be more chance for contact, and you want to be prepared for that,” he suggests. Given the evidence on the first lap of this year’s 24-hour race, where the #8 Toyota took a solid hit to the rear from the #708 Glickenhaus and survived, this approach was vindicated. Another significant difference between the Hypercar and old LMP1 is the suspension design, with the regulations now outlawing the use of tools such as inerters and interlinked suspension systems – both of which featured on the TS050. “It really is back to basics,” says Litjens.Despite having fewer tools in the box to control the chassis, and with it the aero platform, Litjens points out that greater allowances in other areas of the rules mean this is far from an insurmountable problem. Specifically, greater aerodynamic freedom has reduced the need to compromise the suspension geometry to accommodate aero performance features. “Of course, you still want to keep the platform as stable as possible, but you do have a bit more freedom to play with the kinematics of the suspension. If a suspension leg ends up disturbing the aero a bit, you have freedom to compensate for it in other areas to stay in the FIA [performance] window,” outlines Litjens.
Aero freedom
Hypercars are limited to a single bodywork specification across the season, including Le Mans, where previously teams would run a specific low-drag aero kit. As a result Toyota’s aerodynamicists have had to make compromises that were not required in the past, to ensure the package worked across as wide a range of conditions as possible. Describing its approach to the aero, Litjens says, “You stick with a base that you know, especially as we are only allowed one adjustable device, and still have to go to different circuits, from Le Mans to Portimão.” When asked whether Toyota ever thought about going for a wingless design similar to that shown off by Peugeot on its 9X8, Litjens notes that the approach was never discussed. “We felt it [a rear wing] was the easiest route to take and didn’t even think about getting rid of it.”
For the BoP process, the GR010 had to be tested by the FIA at Sauber’s wind tunnel in Hinwil, Switzerland. Toyota did the majority of its aero development in the TMG (Toyota Motorsport Group) tunnels using a scale model, with final validation at full scale. However, the use of a different tunnel for BoP had the potential to cause issues if Toyota’s own results diverged from those of the FIA. “Luckily, we were not too far out, because you only have one day [for the FIA sign-off]. If you turn up and are completely outside the window, you will struggle. We made sure we had some options available to tune things if we needed and were okay,” says Litjens. The regulations set an aerodynamic efficiency target of around 1:4 L/D, although this was upped slightly in a late revision to the rules. To assess each Hypercar design, they are run at Sauber across a wide range of ride heights, airspeeds and yaw angles to create a comprehensive aero map. Once a car is passed, the FIA conducts a 3D scan of the bodywork to create a reference set of CAD data. At any point in the season, the FIA can seize a car and rescan it to check it remains in compliance with its original homologation.
Powertrain simplification
Toyota has retained the same 3.5-liter, twin-turbocharged V6 engine layout it used in the TS050 for the GR010, but, says Litjens, it is an all-new design, which more closely represents the company’s road car offerings. Without the need to hit stringent fuel usage targets, there was less pressure to focus on outright efficiency. Similarly, the inclusion of a minimum engine weight of 165kg and CoG of 220mm lowered the emphasis on reducing the mass of every part. Initially, the Hypercar regulations also defined minimum weights for the hybrid system, and as such, Toyota worked to these. It also kept a close eye on costs, with Litjens stating that the battery technology, for example, is now much more closely related to that found in the road cars.
However, in one of many regulatory about-faces, the minimum weight requirement for the hybrid was removed – the only limitations being a maximum RPM of 25,000 and a minimum laminate thickness of 0.1mm – but Toyota was already committed to the weight-constrained design and could not further optimize its solution. On the TS050, Toyota worked with separate suppliers on its hybrid motors, Aisin providing the front unit and Denso the rear.
In an interesting move, the new car’s hybrid (by regulation it only has a front motor) is now a collaborative effort between the two companies. The management of the hybrid system’s contribution to the total vehicle power needs handling in a different way to that of the previous LMP1 class. In Hypercar, the total output (IC engine and MGU) is fixed at 520kW. It was initially due to be only 500kW for Le Mans, but this was revised following the opening races of 2021 in order to increase the gap to the LMP2 class.
As to whether or not the energy management knowledge gained in LMP1 was relevant to the new hybrids, Litjens says, “It’s 50:50. Energy management, state of charge of the battery and how it reacts under load are the same. But what is different is that before, you had your combustion power and then, when you needed more, the hybrid on top, which made it easier for the drivers to overtake. “Now, you have the maximum power and it doesn’t matter whether you are taking 400kW from the engine and 120kW from the hybrid, or any other combination of inputs, so the controls there are quite different [compared with the LMP1 hybrids].”
That’s not to say that deployment strategy becomes irrelevant. Litjens points out that the contribution of the hybrid motor provides an instant torque addition, which is particularly beneficial on corner exit. He also highlights that the IC element of the powertrain must always be capable of producing the maximum output “in case you end up in a situation where you have run out of hybrid power”.
The upshot of the new rules is that the upper bound on power output must be tightly respected, as must the homologated power curve. With torque sensors mandated on all driven axles, the FIA is able to monitor performance in real time and the tolerance provided is narrow. Incidents such as skipping over a harsh curb could easily cause an unforeseen torque spike, placing the team in line for a penalty. “In the past it was not really an issue, except for reliability. But now, for sure, you need to be very careful, and have to spend some effort on those controls,” says Litjens.
Of course, racing being what it is, the margins are there to be pushed and he readily admits that any safety margin needs to be as small as possible to be competitive. Development hurdles The first GR010 prototype ran on its maiden test in October 2020. Toyota’s target for any new car pre-Le Mans is to complete at least four 32- to 36-hour endurance tests. Covid-related travel restrictions made achieving this tricky, compounded by snowfall at a session in Portimão, necessitating scheduling an extra test.
Conscious that its Le Mans ambitions had been scuppered in the past by issues that could have been worked around (such as its ECU failsafe shutting down the motor on Nakajima’s car in 2016 when it could have run back to the pits), Litjens notes, “It is not just pure development testing, but also working on the ‘what ifs’. We have learned over the years to focus on reliability but also have systems ready to react if something fails.”
So how does a team win in a BoP class? In Litjens’ opinion, a competitive advantage is found in being able to hit the upper end of the performance window across all conditions. “You have to be consistent – the car, the drivers, in all conditions. You can have a car that is perfect aerodynamically in free air, but if you end up in traffic, you also need to be as stable as possible.” This consistency is achieved in many ways that go beyond the pure mechanical design of the car. For example, he points out that if particular surfaces prove to be susceptible to debris pickup over the course of a race, this can damage aero performance and must be mitigated.
Ferrari caused something of a stir when it announced it would return to the sharp end of sportscar racing, having not fielded a works prototype team since the 1973 312 PB. The company chose the Hypercar route, as is befitting of a marque with its history.
When the car was officially launched, John Elkann, Ferrari executive chairman, remarked, “The 499 P sees us return to compete for outright victory in the WEC series. When we decided to commit to this project, we embarked on a path of innovation and development, faithful to our tradition that sees the track as the ideal terrain to push the boundaries of cutting-edge technological solutions, solutions that in time will be transferred to our road cars. We enter this challenge with humility, but conscious of a history that has taken us to over 20 world endurance titles and nine overall victories at the 24 Hours of Le Mans.”
Based around an in-house developed and built carbon tub, the 499 P combines the experience of Ferrari’s longstanding GT team with some of the engineering might its F1 operation brings to bear, particularly in hybrid system design and management and virtual car development.
According to Mauro Barbieri, Ferrari’s endurance race car performance simulation and regulation manager, the development timeframe for the car was compressed, particularly the track testing element. “The on-track program has been quite squeezed. In order to be able to join the championship in Sebring [2023],” he says. As a result, considerable effort was put into the virtual development program. “We did quite a lot of activity while designing the car and while producing the parts with the driving simulator to test different possibilities, different solutions, and I think we did quite some job on the virtual side.”
The team has access to both the DIL simulator used by the GT operation and also Ferrari’s older F1 simulator (replaced last year). By being able to work on setups in the sim, the focus of the six-month track test program could be on reliability. Barbieri says, “In terms of setup optimization, we didn’t push that much. And maybe on that side, we could, we could improve still a bit. And hopefully close the gap with the cars in the front.”
Giving more detail on the use of the DIL simulator, Barbieri explains, “With the driver-in-the-loop simulator, we were trying to optimize the suspension, the aero maps that we were getting from the wind tunnel and trying to give development direction for the following sessions based on how the car was behaving at that time.”
Aero/styling balance
Though not going to the same extreme as Peugeot, the 499P was always going to carry a strong brand identity. “Anything that we produce in terms of race cars, the external design is always shared between the aerodynamic engineering and the style department, the design department of our company,” notes Barbieri. “That’s true for the LMH car but also for the GT3 cars as for the road cars, so we had quite a few loops between, let’s say, the aero engineers and the designers to make sure that we’re going to design a car that was not just fulfilling all the requirements, but that was also satisfying the eye.”
This, he adds, did not really place any limitation on the aerodynamic design thanks to the BoP regulations. “The downforce and drag limits, let’s say set by the technical regulations, are not so difficult to achieve. And we also had some room to try and optimize the aero itself. For our needs I wouldn’t say that it has been in any way a constraint. It’s just been quite a few loops because the pure aerodynamic solution had to be slightly reviewed.”
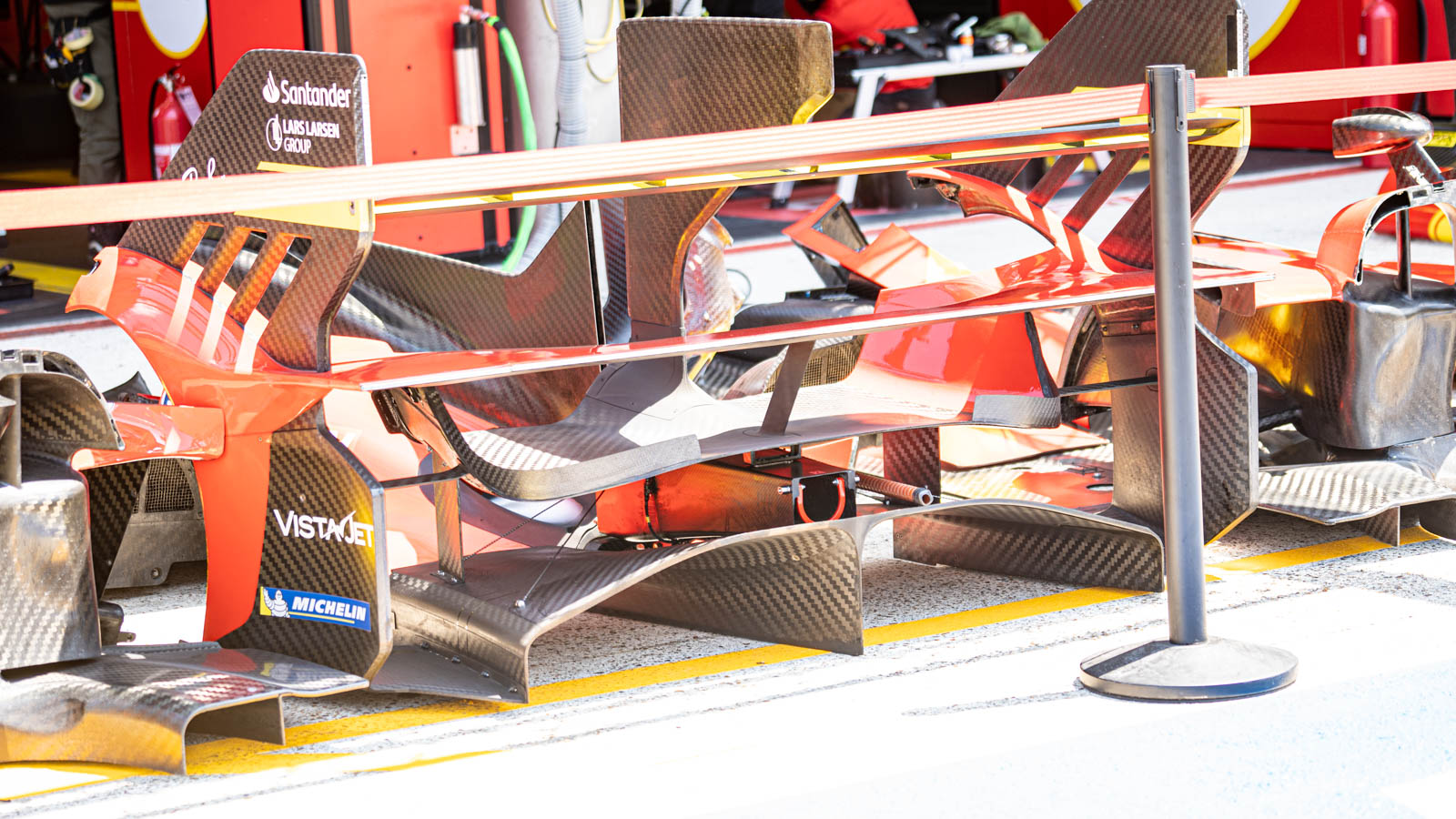
Ensuring there was sufficient flexibility within the aero package to cover the various track types experienced over the WEC season was a prime consideration, particularly given that once homologation was complete, the package could not be changed. For this reason, Barbieri says, “We choose to go with the rear wing as an adjustable aero device to get to have a big span in terms of downforce level and drag level to try and be able to optimize the car at every single circuit.”
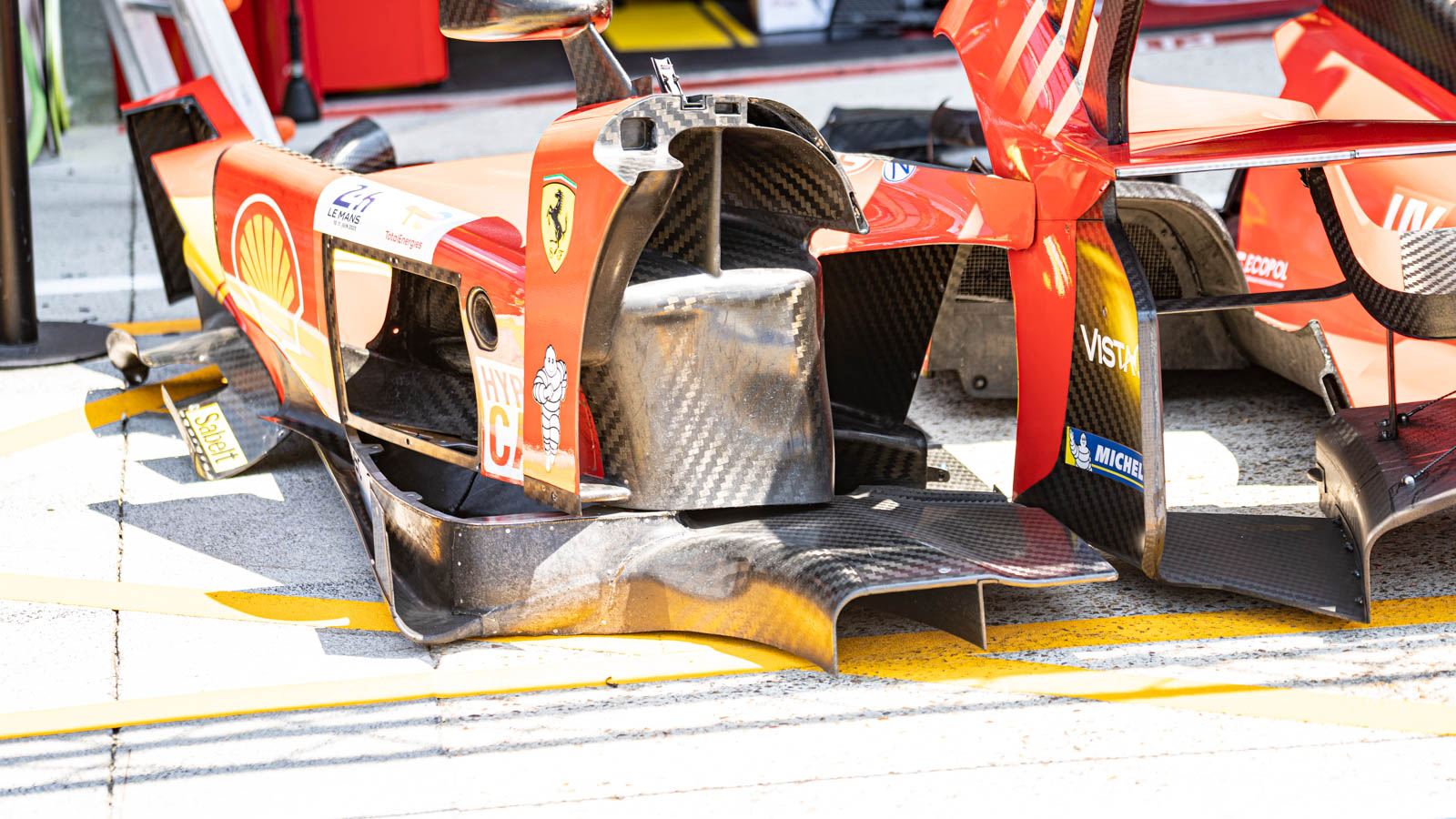
He also points out that the rear wing is more useful than an adjustable front element, particularly when it comes to adjust setup throughout a race. “For example, one thing that you want to take into consideration during Le Mans is the transition from day to night, the temperature getting colder,” suggests Barbieri. “With the track going toward understeer, you might want the [adjustable] front wing to raise a bit the front downforce level. But then, if it rains, you normally want to go rearwards with downforce to give the driver a bit more confidence. But maybe that’s not what you want to do, because if you reduce the front wing to move the downforce rearwards, you might reduce the overall level of downforce. Normally the front wing is almost free in terms of drag. There are many aspects that you try to consider and probably you cannot tick all of the boxes, but we try to tick the ones that we believe were the most important.”
Powertrain development
The 499P’s hybrid powertrain combines a mid-rear power unit with an electric motor powering the front axle. The latter, alongside the battery, is derived from solutions developed in Ferrari’s F1 program.
The ICE has a maximum regulation-limited output to the wheels of 500kW and is derived from the roadgoing twin-turbo V6 family found in Ferrari’s road cars and the 296 GT3 race car. For prototype duties, the engine has undergone a thorough overhaul by Ferrari’s engineers, aimed both at prototype specific adaptions and reducing its overall weight. The key difference is that in the 499P, the engine is a load-bearing element (in the GTE car it is mounted on a subframe).
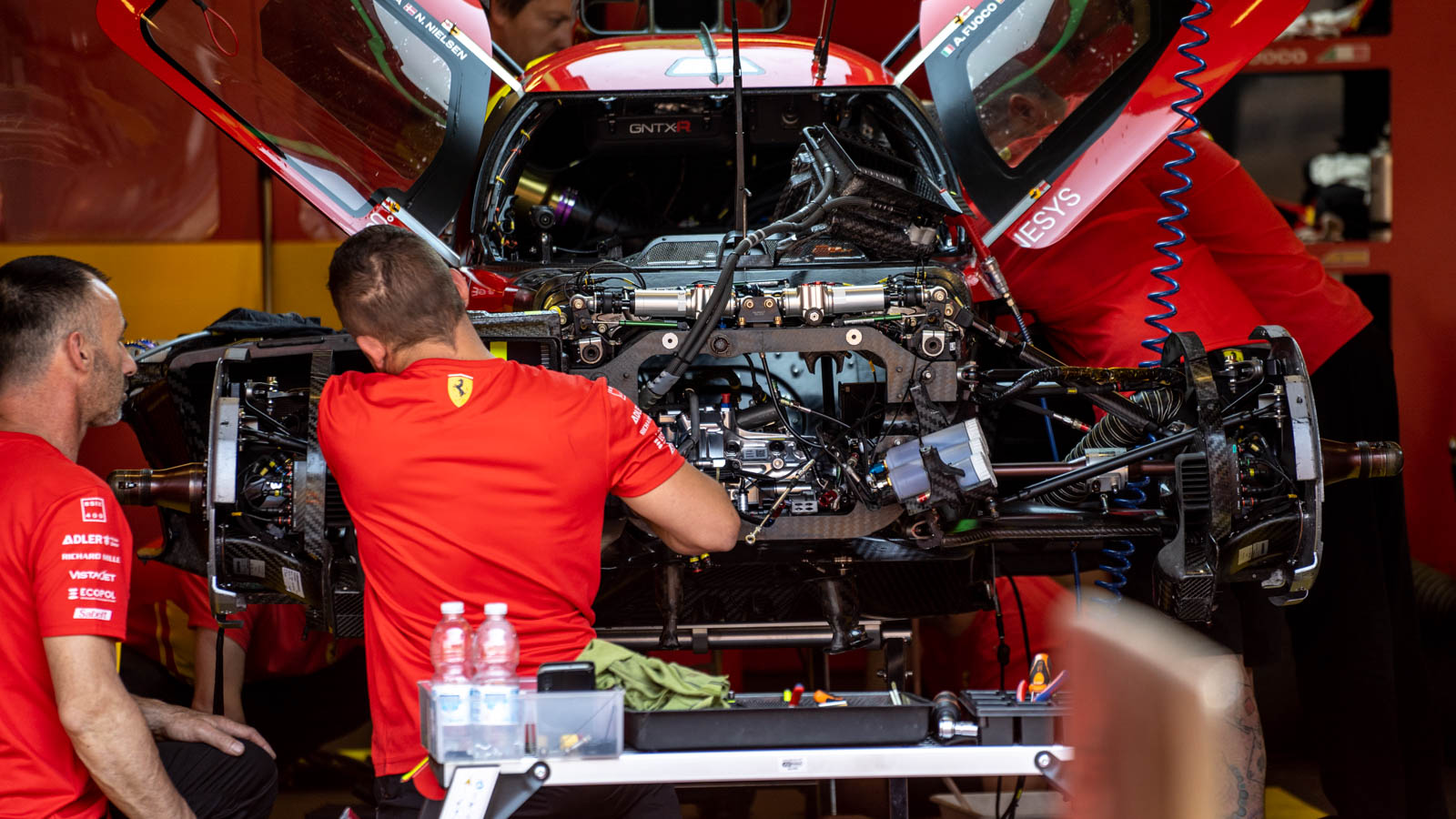
The ERS system has a maximum power output of 200kW and the front-mounted MGU is equipped with a differential and recovers energy under braking. The battery pack, with a nominal voltage of 900V, benefits from Ferrari’s experience in F1, although it was purpose-built for the project. The 499P’s maximum power output is achieved either via a combination of hybrid and ICE power or, where needed, purely by the ICE, with drive delivered to the rear wheels via a 7-speed sequential gearbox.
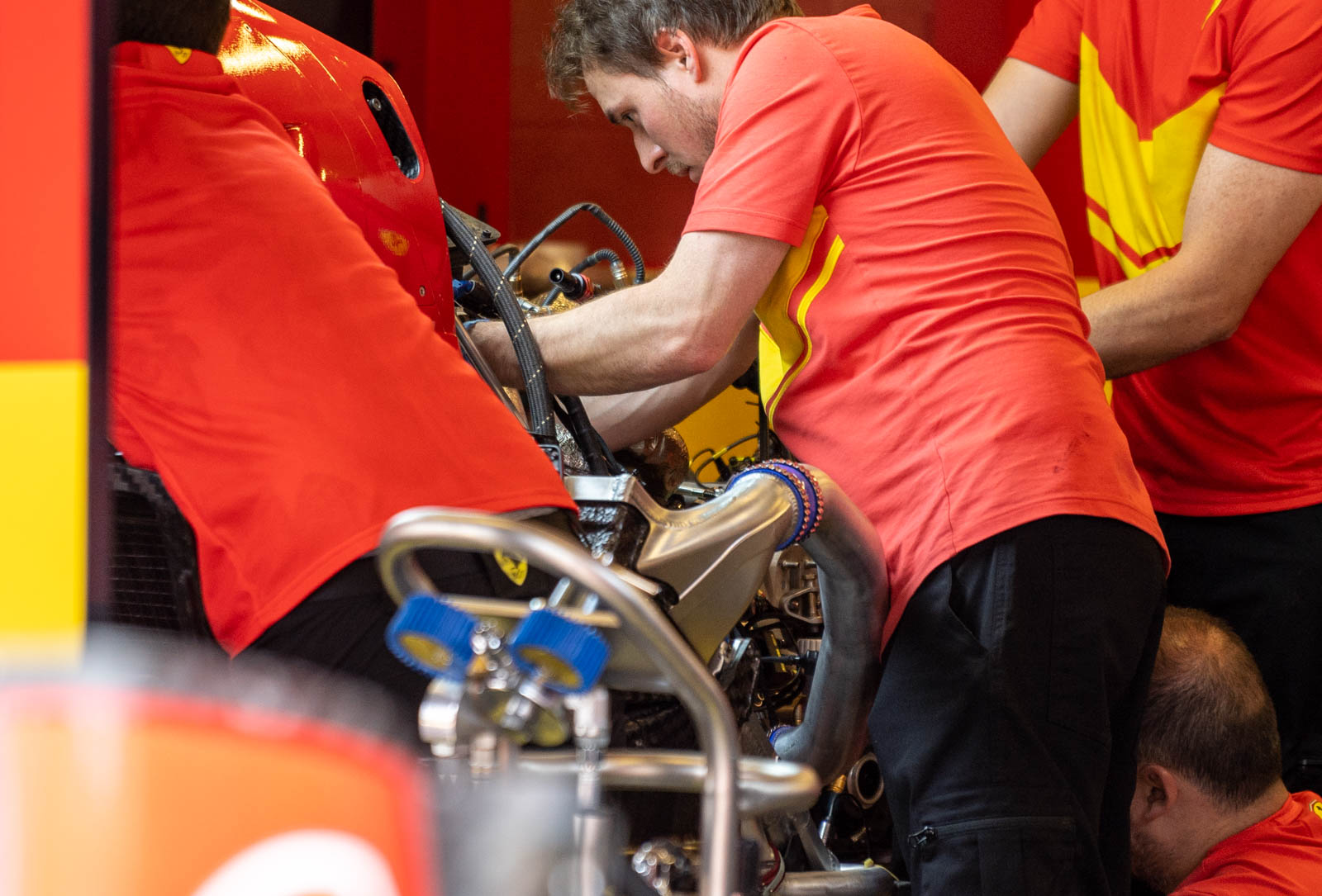
With plenty of customer experience on the sportscar side, Ferrari opted to work with Bosch on the engine and vehicle electronics systems, rather than with Magneti Marelli, which is a technical partner on the F1 project.
F1 assistance
It would be easy to assume that the sportscar team could rely heavily on the F1 department during the car’s development but given the intensity of competition in the latter series, there were limits to what resources could be diverted.
However, it was able to leverage some of the F1 outfit’s advanced, in-house developed tools. “With collaboration with the F1 team let’s say, we have separate departments. But this doesn’t mean that we don’t share a lot of things in terms of software, in terms of know-how, in terms of exchanging potential solutions in the car,” observes Barbieri. “From the outside, it might look like we’re not sharing that much. But in the end, we are the same company, the same family.”
The Cadillac brand last competed at Le Mans in 2002 with the LMP 01, running in the LMP900 class. Since then, the marque has seen considerable success in IMSA, through the Daytona Prototype and DPi eras. With the arrival of convergence between LMDh and Hypercar, it was a logical step for the brand to return to La Sarthe.
“Cadillac is excited to build on its racing legacy by competing against the very best internationally and at one of the world’s toughest races,” said GM sportscar racing program manager Laura Wontrop Klauser. “We’re proud to be representing the United States and the Cadillac V-Series.R is a great continuation of our racing heritage.”
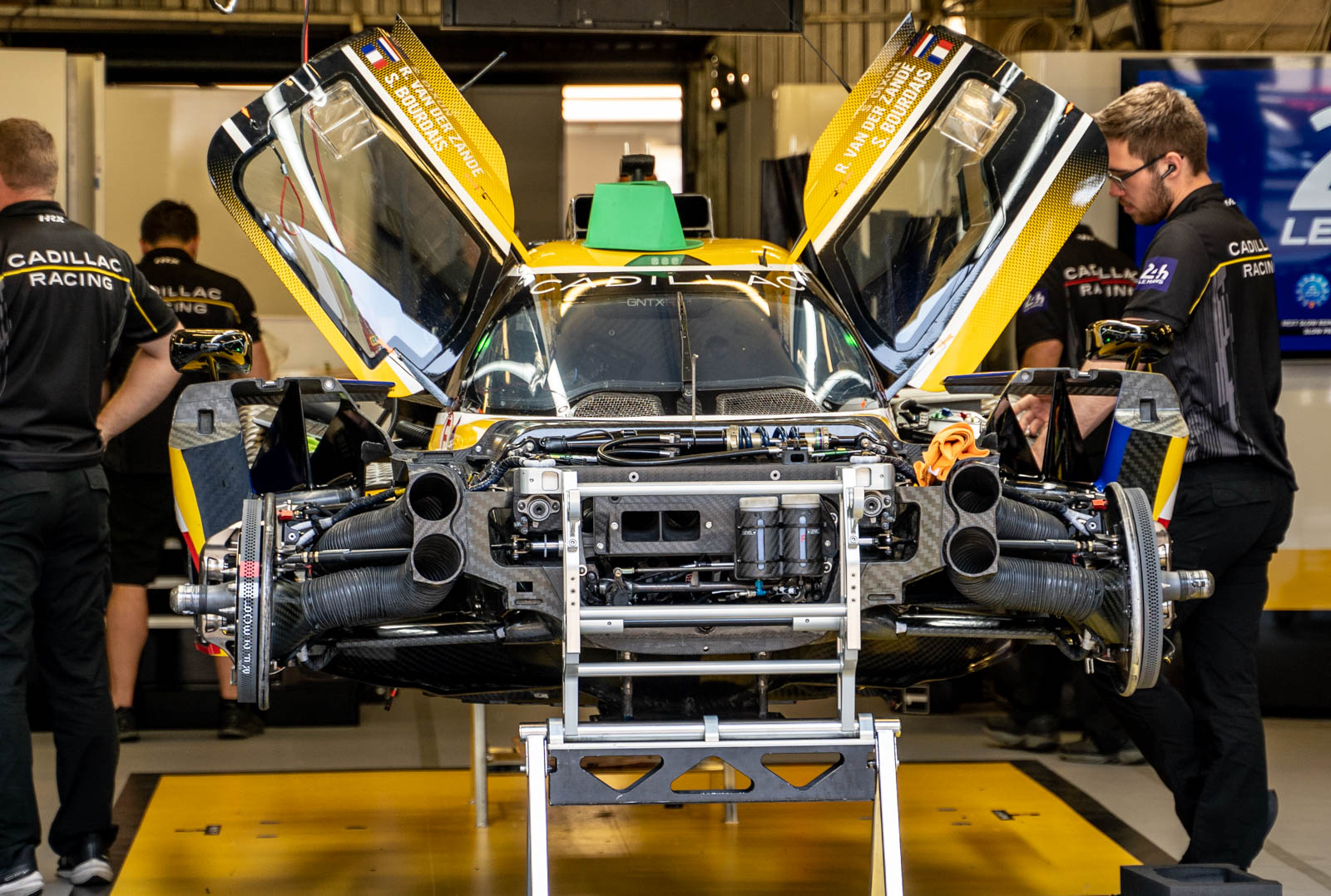
Work on the V-Series.R commenced as soon as the agreement was agreed between IMSA and the WEC in 2020, with Cadillac continuing its relationship from DPi with Dallara as chassis supplier. The LMP2-based chassis is endowed with bodywork developed jointly by Cadillac Design and Cadillac Racing.
Speaking to PMW at Le Mans, Klauser notes that the established relationship with Dallara was key to delivering the LMDh car on time given a compressed development schedule: “Part of doing any of this is you have to trust the people that you’re working with. And trust doesn’t just start from nothing, right? You earn that over time.”
She remarked that many of the Dallara team that developed the DPi chassis also worked on the new car. “A lot of the engineers that supported in DPI came into LMDh, and even some of those who supported us in the development [of DPi] came back to do the development with us in LMDH. They were familiar faces. So it was really nice to go in there knowing the people we were working with. Knowing that when I say I’m going to do something I follow through, when they say they’re going to do something they follow through. That was pivotal.”
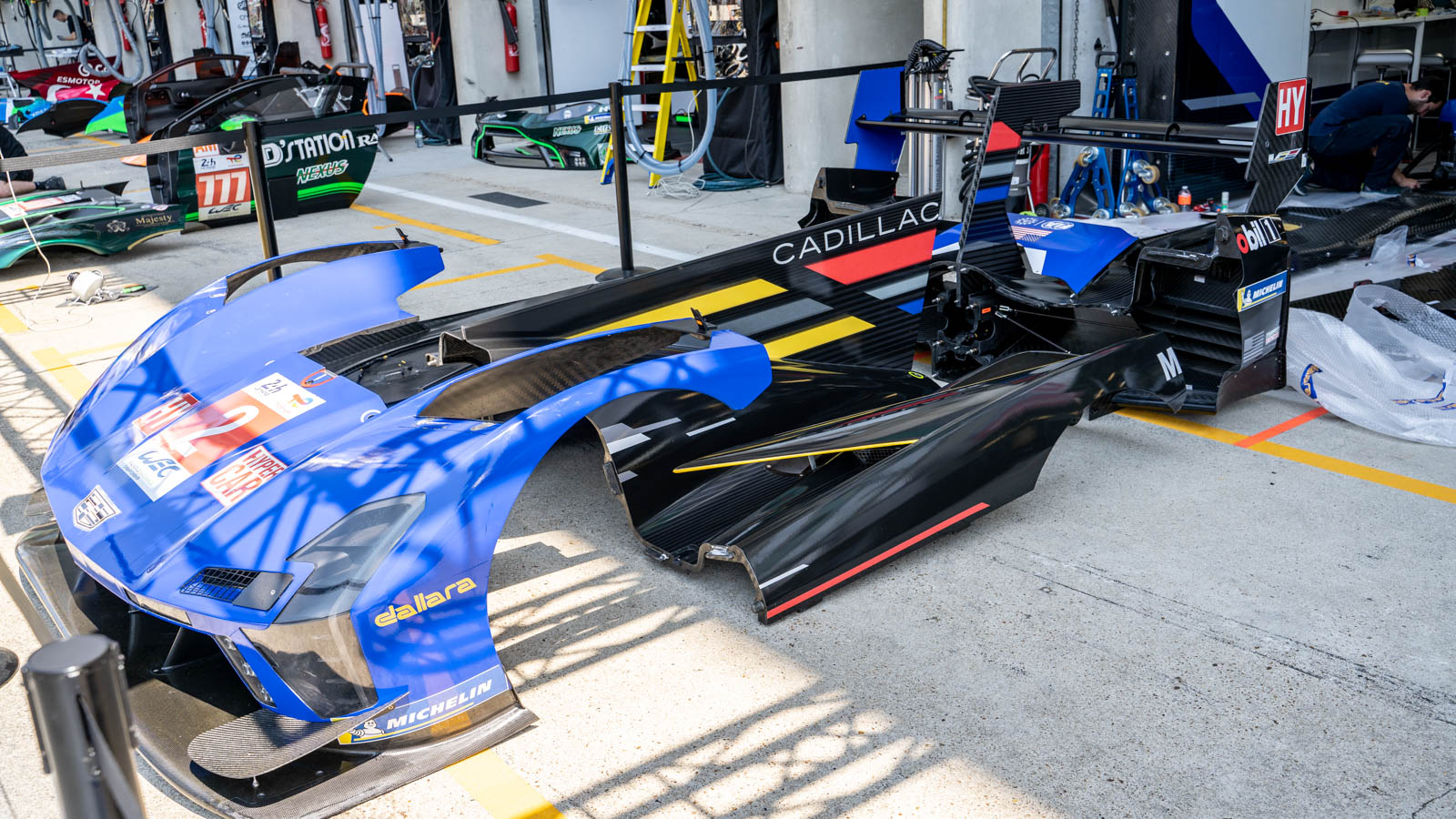
The guiding principles for convergence of the top categories of endurance racing in IMSA and the WEC were announced in 2020. Design and development of the new race car began immediately.
The race car incorporates distinctive Cadillac design elements, such as vertical lighting and floating blades but styling cues from the roadcar were incorporated across the bodywork thanks to a close cooperation between Cadillac Design and the racing outfit and Dallara.
Klauser says that the level of cooperation between the roadcar and race teams was fruitful: “It’s similar to what we did with DPi, the production Cadillac design team worked hand in hand with the Dallara just like our engine team was working with them to create the race car.” There was a free flow of ideas back and forth between the two groups. “We got the initial preliminary sketch [from Cadillac Design]. Dallara took it, evaluated it, they pushed back on some things, they opened up on others, it was actually a really great integrative exercise. You know, no one came in saying ‘I’m right, you’re wrong’. It was, ‘Hey, let’s see, let’s look’.
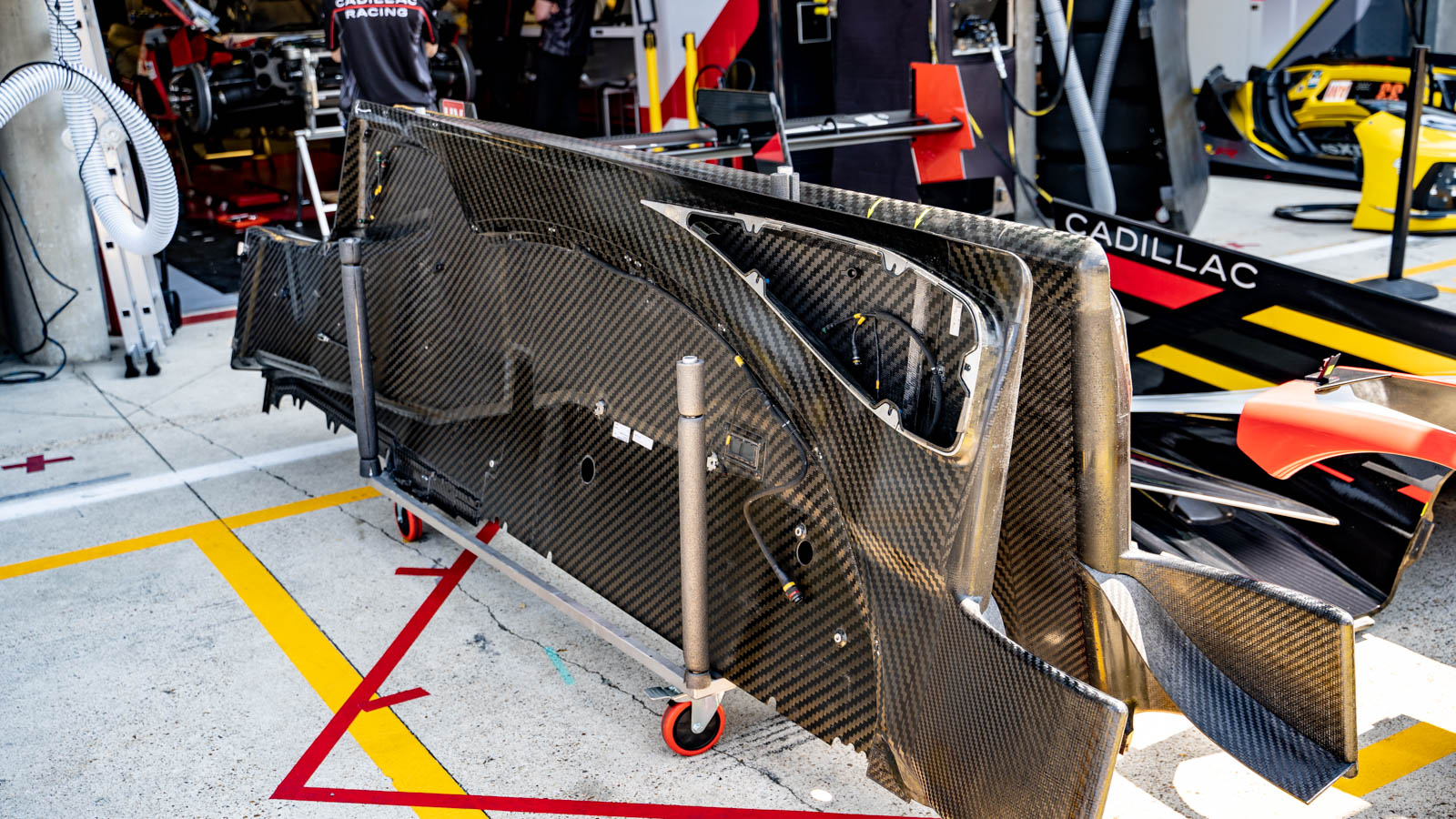
“With some of the features on the car when Dallara first saw it, they were a little like, ‘Uh oh, what is this?’. But we ran it through the aero and did everything we’re able to. We found some unique things that were good, that I think no one was expecting, and then also found some ideas that design had that we just had to slightly morph into something that would make a better race car. We ended up with a really nice balance of form and function.”
The car is propelled by a new 5.5L DOHC V-8 engine – prepared by GM’s Performance and Racing team centered in Pontiac, Michigan – which is based around the current Corvette motor. Much of the team’s development work centred around pulling weight out of the unit to make it more suitable for use in a prototype, while also adapting it to run with the WEC specification renewable fuel (which appears to have a lower knock limit than traditional race fuel).
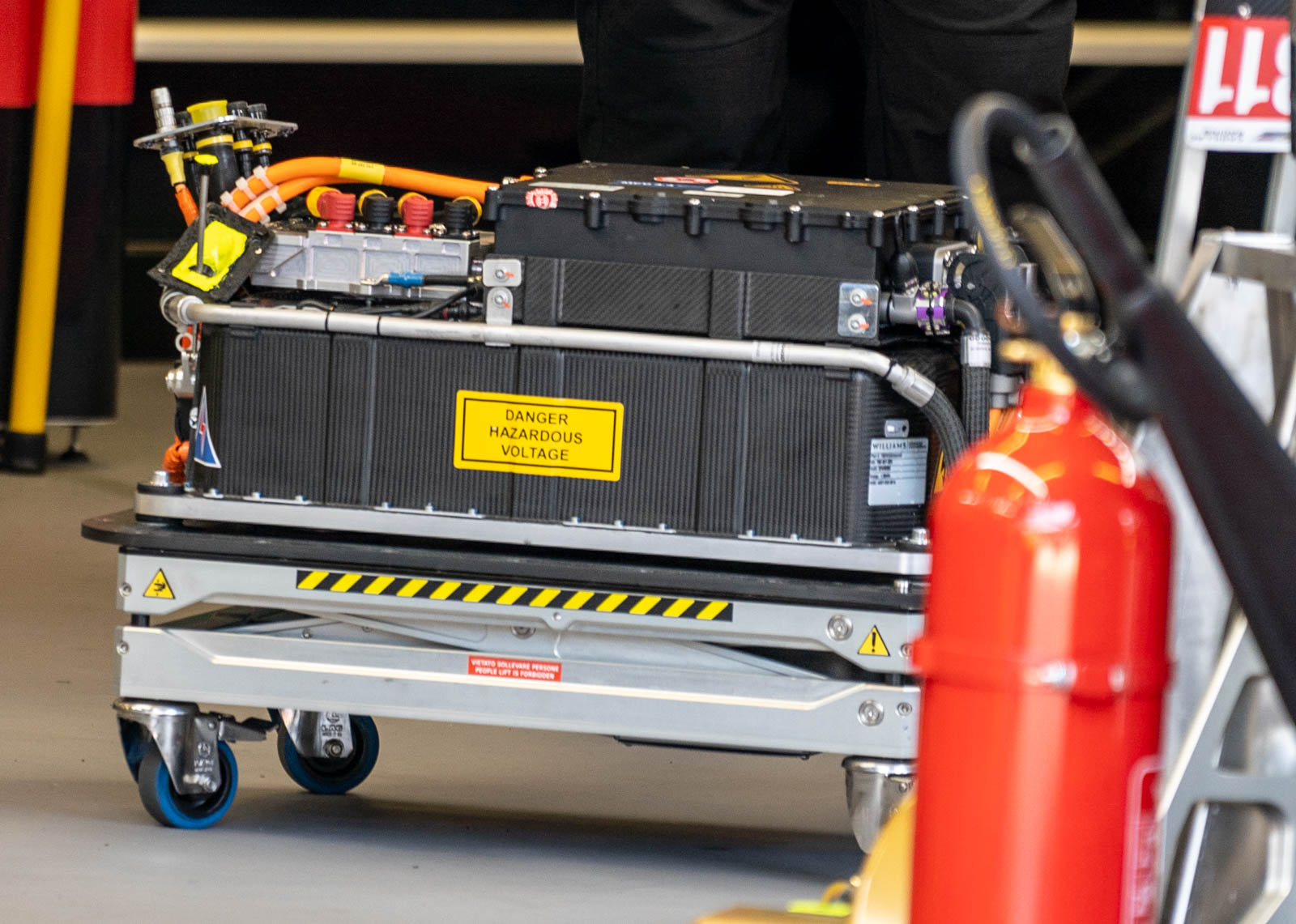
The spec energy recovery system was developed by Bosch, Williams Advanced Engineering (now WAE) and Xtrac. The development of the hybrid was fraught with problems early on, with the IMSA manufacturers taking a collaborative approach to solving these issues (see the 2022 interview below). Klauser says that this has continued into 2023, even though the teams are now locked in competition.
“We are very good about sharing the information that is important for the spec system that everyone needs to know. Then information that is not part of the spec system is ours. And really, with the hybrid, there’s nothing to be gained, only to be lost with knowing something that the other ones don’t, mainly because any changes have to be across the board. It’s all about reliability, durability, the hardware, any changes, that kind of stuff is what we’re working with, we don’t really get much performance out of that. The stuff where there is performance for us is in our engine calibrations, in how everything mates together. And that belongs to us.”
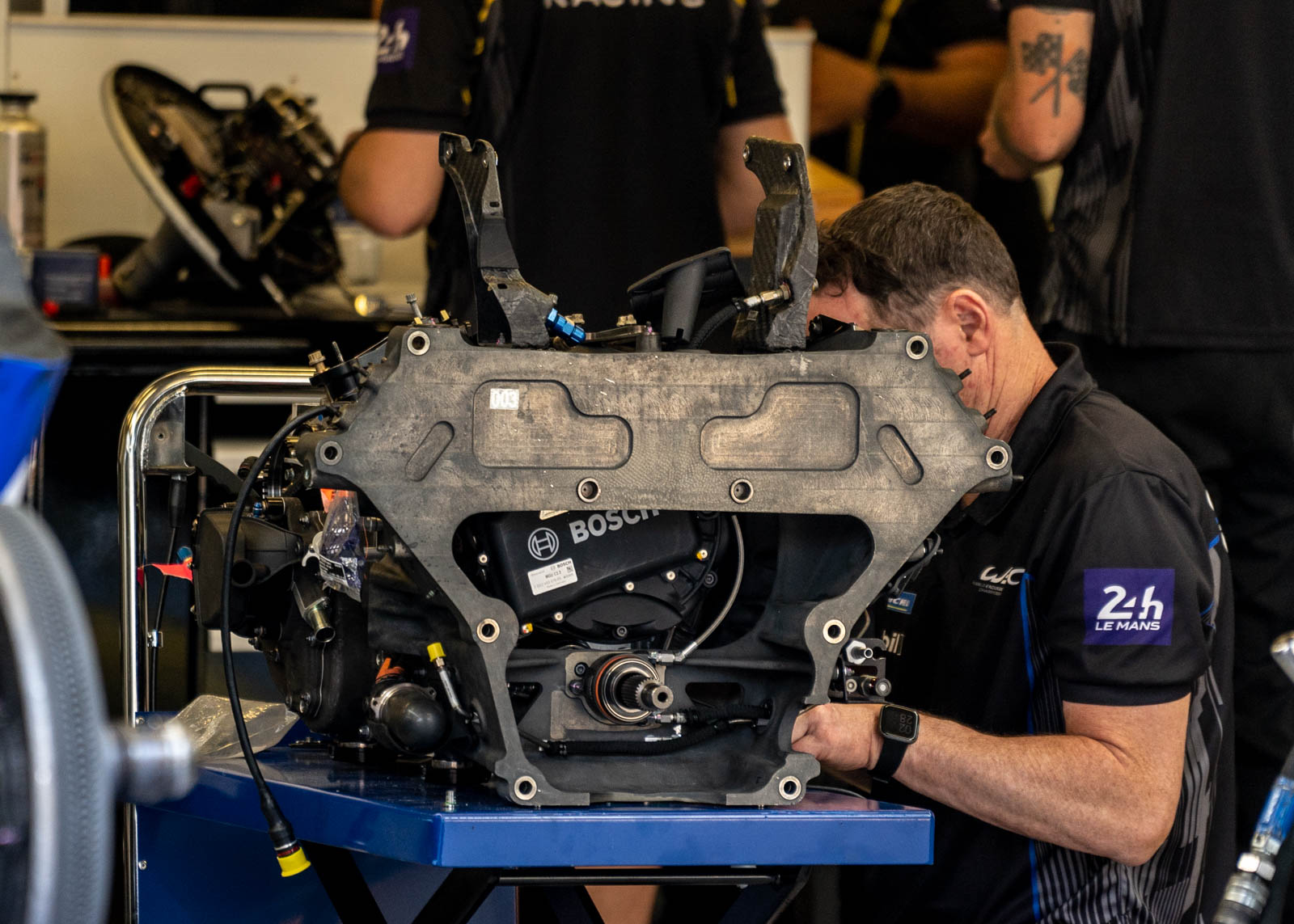
On-track development of the car began in July 2022 with it logging more than 12,400 miles (20,000km) on racetracks in the USA, leading into the car’s debut at the 2023 Daytona 24. Since then, the Caddy has proved, by and large, to be reliable, and next to Toyota and Ferrari, is one of the favourites for the Le Mans win.
[accordions]
[accordion title=”Interview with Laura Wontrop Klauser” load=”hide”]With Cadillac having finally released a full view of its Project GTP Hypercar LMDh racer, PMW caught up with Laura Wontrop Klauser, GM’s manager for sportscar racing projects, at Le Mans, to find out how the project is progressing.
Running on a Dallara chassis, the GTP Hypercar will be powered by what Cadillac describes as an all-new 5.5L DOHC V-8, paired to the spec Bosch/Williams/Xtrac-developed hybrid system.
According to Klauser, the development of some areas of the car, particularly the hybrid system, has seen a high degree of cooperation between manufacturers: “The relationships across the board are great in terms of the LMDh platform. It has given the opportunity for all of these OEMs to sit down at the table together regularly, and to meet and to work through issues that affect all of us together. In the case of LMDH, we’re sharing that spec hybrid system. So the development and all that has been a shared entity among us, and it’s making all of us stronger. It’s also making the process quicker; time is of essence in these cases.”
Reliability and supply woes relating to the spec hybrid have surfaced in recent weeks, and though she wouldn’t be drawn on this subject, Klauser said that the situation on the supply side at least was improving: “We’re definitely working through them [the issues]. At this point, I think everyone has what they need to get started, which is great. Of course, we all wish we had tons of things. But in the world we live in that’s just not an option anymore, but it’s enough that we’re able to keep moving on with our test plans.”
She also highlighted that the collaborative efforts between LMDh entrants were helping to overcome reliability and installation issues, with Porsche’s experience from its early track tests allowing other entrants such as Cadillac to focus on different areas. “By working with each other it keeps us from all having to do the exact same test,” she said. “We’ve been we’ve been doing testing on the dyno and a variety of other in-house tests, whereas Porsche has been more on track. We are feeding all the learnings back to each other so that when we get on track, we don’t have to do the initial things that they had to work around. We already know those so they can move on to the next level.”
The development process in areas such as mapping for the hybrid’s energy deployment is also still something of a moving target. As to whether teams would have tightly regulation-controlled deployment strategies or more freedom to innovate, Klauser said, “That is all still under development. So it changes regularly. I could give you an answer right now, but it might be different tomorrow. That’s all-new territory, so we’re, again, as a unit, trying to understand what the best way is to initiate the application [of the hybrid]”
The Peugeot 9X8 LMH was never going to be ready for the 2022 Le Mans 24 Hours as the French manufacturer originally hoped. Supply chain issues combined with Covid-19 restrictions ensured that the marque’s return to the pinnacle of endurance racing would have to wait another year. In the long run, this was probably for the best.
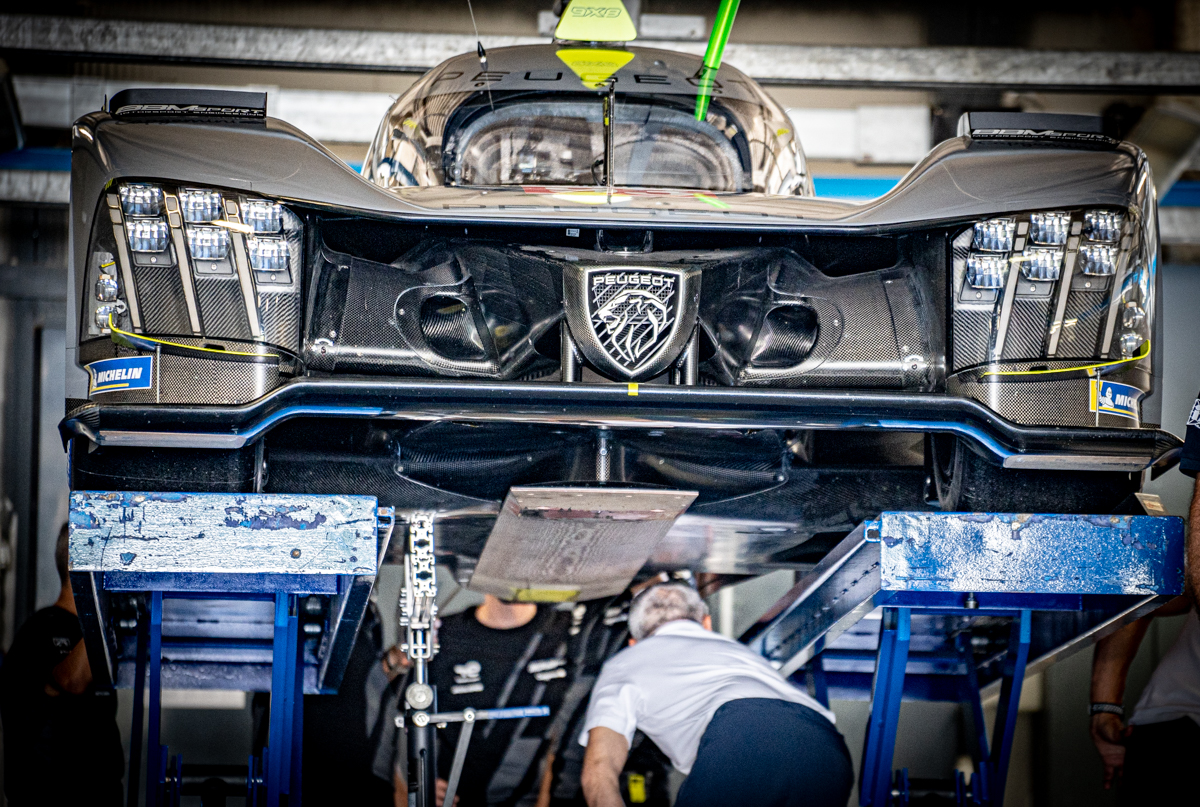
When the car finally made its debut at the 6 Hours of Monza the following month, before completing the remainder of the WEC season, it was clear that not only did it need refinement, but so did the team. A rushed rollout two months earlier would have been unlikely to improve the situation and would have locked Peugeot into a suboptimal homologation spec. As it was, the 9X8 made a good showing in Italy, it was close to the pace and seemingly didn’t display any wayward handling traits. However, neither of the two cars were reliable, and watching Peugeot’s pit operation, it was evident that the team needed plenty of polish before it was on a par with Toyota.
Push to target
When PMW last spoke to Peugeot Sport’s WEC technical director, Olivier Jansonnie, at the 2021 Le Mans 24 Hours, the 9X8’s final designs were about to be released for production and the manufacture of jigs and tooling was being approved. Catching up with Jansonnie in 2022, once again at Le Mans, he highlighted that Peugeot’s timing was unfortunate.
“It was a really tough time as I think every team and manufacturer was trying to do the same thing, there were shortages of materials and components, and on top of that there was still the problem of Covid. It took a massive push from our production department and our smaller suppliers to build the car. We did our first test in December 2021 and that was a very important milestone [to hit].”
Peugeot relied heavily on its simulation program, particularly through 2021, with an emphasis on virtual testing of the car using its driver-in-the-loop (DIL) rig. “It was tough because we were developing our simulation and the car in parallel through 2021 and we had about a year of only virtual development. With the DIL, it is not as good as actual track data, but it is very valuable both for development and running of the car,” remarked Jansonnie.
While it was possible to physically test the 9X8’s powertrain off-track, with Peugeot running an extensive test bench program for both the ICE, hybrid unit and control software, Jansonnie suggested that rig testing of chassis-related components was limited. “In terms of suspension and those areas, it is hard to test what you see on track.” You can apply the load cases you expect to see and make sure they match the simulations and calculations, but there are the load cases you may have forgotten or haven’t foreseen. You will only find those on track, or more specifically, during races.”
Clean lines
The standout feature of the 9X8 is clearly its lack of a rear wing, which caused a few raised eyebrows when the car first appeared. Jansonnie was coy about revealing too much detail surrounding the car’s underfloor design, but explained that the concept was made possible thanks to the greater freedom afforded by the LMH rules compared with LMP1. He noted that the center of the floor was now able to contribute a much greater proportion of downforce than before, though the rear diffuser remained quite similar in performance to the previous generation of LMPs.
Fortunately, scrutineering at Monza afforded an opportunity to look under the 9X8, which revealed relatively modest underfloor tunnels, albeit with some interesting treatment of airflow coming off the front underwing. That Peugeot could do away with a wing was not solely down to regulatory freedom, but also the conservative aero targets set by the BoP and homologation process. Jansonnie quipped, “If we had a rear wing on this car, we would generate more downforce than we could use.”
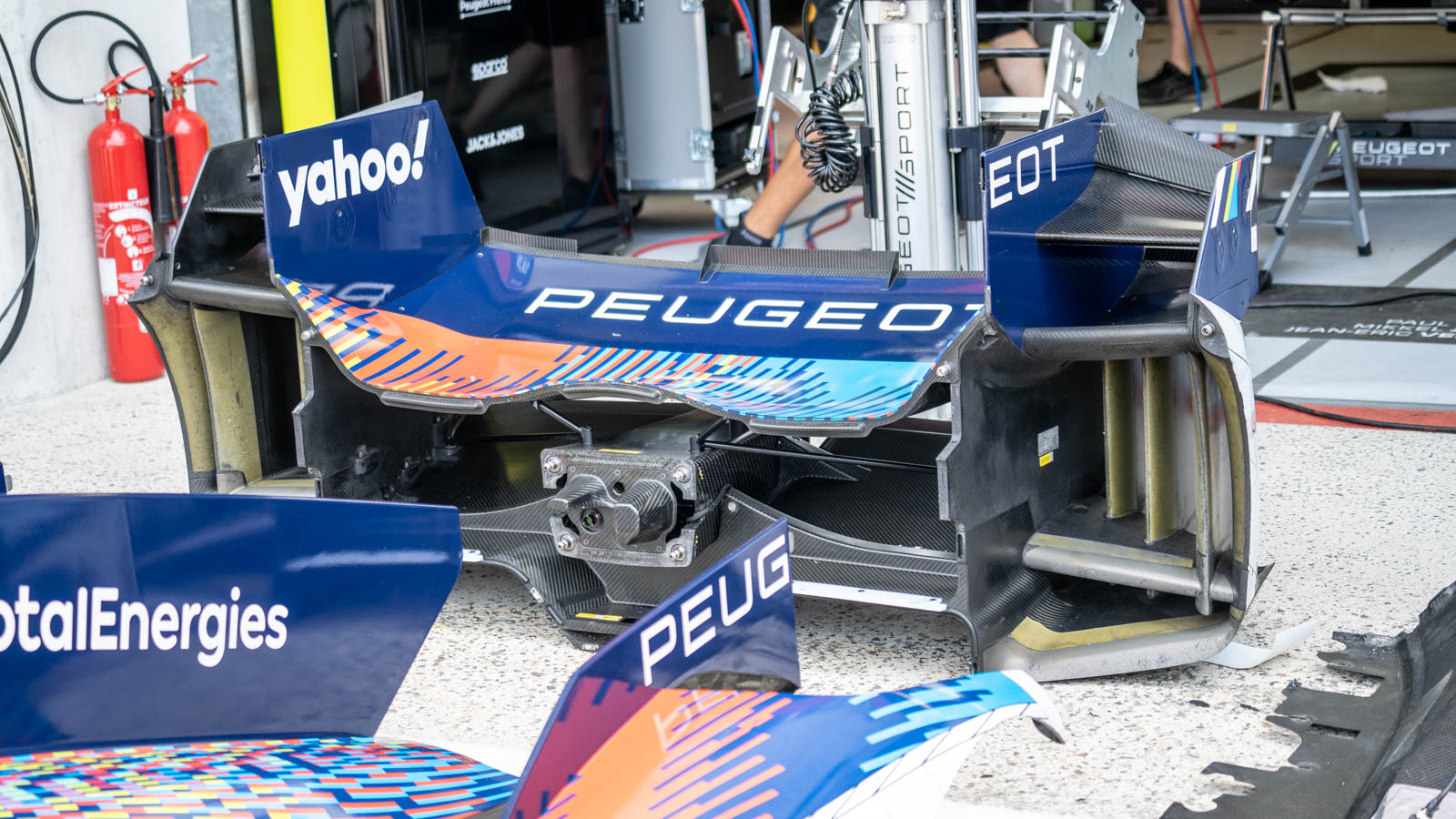
To balance the car aerodynamically, the rules permit a single adjustable device to be used, fitted to either the front or the rear. To this end, the 9X8 features a single adjustable element on the front underwing, which is almost seamlessly blended into the main wing structure. Adjustments are made via securing struts at either outboard end of this section. To ensure that sufficient balance adjustment was available, Peugeot conceived three solutions during the car’s design phase. Jansonnie stated that its primary choice was always an adjustable front element, which showed the best potential in both CFD and wind tunnel analysis.
However, it was only once track testing commenced that its effectiveness could be confirmed. The reserve alternatives relied on the rear Gurney flap that runs along the trailing edge of the bodywork, with options to make this either height or angle adjustable. “With everything on the car, we have a primary option, which is our reference solution, fitted to the car when it hits the track, and backup options. We ascertained when the latest point would be that we could switch direction, but fortunately we didn’t have to go that way,” said Jansonnie.
Observing the car at Monza, which is an admittedly relatively smooth track, requiring low downforce, the car did not seem to display any unpleasant traits. Watching through Ascari corner and the high-speed Parabolica, the 9X8 at all times remained well composed, an observation also reflected by in-car footage. However, the breadth of track types visited over the course of the WEC does appear to have pushed Peugeot’s setup into uncomfortable territory, particularly Sebring (in 2023) where the car struggled over the bumps. As another team’s technical director observed, the car appears to be something of a Le Mans special, at the expense of performance across the WEC season.
In terms of ride height sensitivity being a greater issue due to the reliance on the underfloor, Jansonnie said, “It’s different in the way it behaves, but I wouldn’t say it is more or less sensitive [than a conventional car]. We must have some humility and recognize we have only run on some tracks – but so far, we haven’t found anything that makes it very different to cars we have run in the past.”
Weighty matters
It is notable that the rules do not place any limitations on weight distribution (as is the case in series such as F1); however, once a car is homologated, the distribution can only be adjusted by ±0.5%. This has the potential to create problems related to BoP, which allows for a car weight of between 1,030kg and 1,080kg, meaning Peugeot and all other teams must account for potential additional ballast placement early in the design stage, while staying within the distribution window.
“It’s a very difficult exercise and you have to plan well in advance of homologation,” pointed out Jansonnie. While not willing to divulge its exact weight balance, Jansonnie suggested that the car was designed from the outset to run equally sized tires all around (31/71 x 18), as was specified by the rules for hybrid cars when Peugeot commenced work. The entire concept therefore centered around making these tires work, which he said requires a near 50:50 weight distribution. However, the rules were later changed to allow 29/71 front and 34/71 rear tires, which Toyota took advantage of with its reworked GR010 in 2022. Clearly, the use of a larger rear tire benefits both grip and wear over a stint.
For Peugeot, the change came too late. “We would have had to redo everything, and we wondered for some time whether we should accept a delay in the project and start over again,” Jansonnie recalled. In the end, it stuck with the previous tire specification and Jansonnie said it was assured that performance would be balanced regardless of tire size, saying, “We are all in the same boat and we have to make it work.”
With a hefty minimum weight, it was apparently relatively easy to design a car with scope for ballasting, and Peugeot had an easier job than Toyota in this aspect. The latter’s design tied into earlier rules relating to minimum weights for components such as the hybrid motor. These constraints were later removed, with Peugeot early enough in its design cycle to take advantage.
Outlining Peugeot’s approach, Jansonnie said that it started out with the lightest concept it could (within reason), then reinforced areas that presented problems during testing. “The car has got heavier through testing, but we feel it is much better to start with a light design and reinforce, rather than the other way round. Shaving weight off a car is very difficult and expensive. It’s a bit scary to begin with because you keep breaking parts until you reach the right level,” he explained, adding the caveat, “Maybe we are still not at the right level: only racing will tell.”
Decoupled suspension
One area of note on the 9X8 is its front suspension, which the team was at pains to keep covered up during the car’s debut. However, PMW was able to obtain clear photographs, which suspension engineer and motorsport consultant Andrea Quintarelli was kind enough to provide comment on.
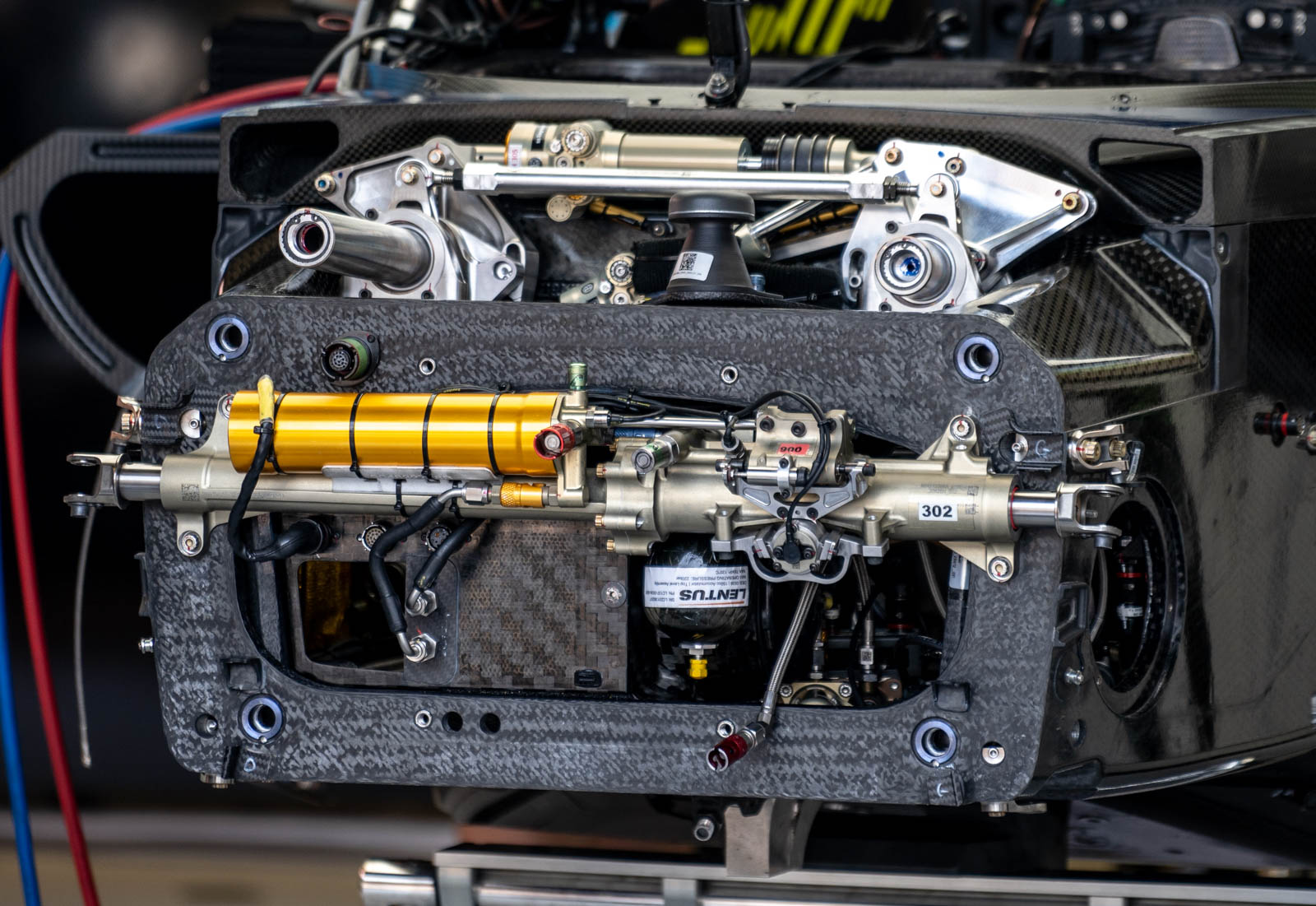
“Peugeot seems to have adopted a concept that appeared on F1 cars some years ago, which seeks to decouple roll and heave. The layout employs two rockers, one on each side of the monocoque, with a heave damper mounted on top and a roll damper installed diagonally between them. In heave, when the two rockers rotate in opposite directions, the third damper is compressed and its length is reduced; in this scenario, the roll damper does not change in length and it does not produce any action.
“In roll, when the two rockers rotate in the same direction, the opposite happens: the heave damper does not change length, because the pickup points where it is attached to the rockers move more or less horizontally, an equal amount and in the same direction. The roll damper, on the other hand, is compressed or extended, due to it being attached to the top of one rocker and to the bottom of the other, thus its length changes when the rockers rotate [either] clockwise or counter-clockwise. The end result should be an effective separation of damping control in both heave and roll.
“Roll is likely controlled by an anti-roll bar, located on the lower part of the monocoque. A neat feature is the rod that connects the two torsion bars via mounting ‘ears’. The two torsion springs do not appear to be grounded on the monocoque, which would provide a wheel rate as a consequence of them twisting relative to the chassis.
“Rather, they are locked together via a rod. This effectively neutralizes them in roll when the two bars, rotating more or less equally and in the same direction, do not experience any twist. In heave, the two rockers twist their respective torsion bars in opposite directions, counteracting the rocker’s rotation, providing a pure heave spring effect. Another pleasing side effect of this design is that two torsion bars of different length and stiffness can be used on either side of the car, in order to achieve the desired overall wheel rate.”
A full, indepth description of the system can be found on Andrea’s blog, here.
Powertrain
The 9X8 runs what Jansonnie said is an entirely in-house-developed powertrain, consisting of a twin-turbocharged, 2.6-liter direct-injection V6, married to a 200kW front-mounted electric motor-generator. As per the LMH rules, total output of the powertrain is limited to 500kW regardless of the combination of ICE and hybrid used (the rules had initially stated an output of 580kW but this was dropped to help alignment with the LMDh rules).
Initially, the rules also set a minimum weight for the engine of 180kg, but when the power requirement was lowered so too was the weight of the engine, to 165kg. According to Jansonnie, development of the ICE drew on Peugeot Sport’s experience stretching right back to the diesel 908 LMP1 days, with a target of producing a compact and power-dense engine and transmission, which would afford greater packaging freedom at the rear of the car.
“Even though the 908 was a completely different concept we were able to carry some ideas over from that time,” he said, adding, “There are also elements from our WRC and WRC projects; for example, the engine’s combustion chamber concept. It is a melting pot of ideas from other projects in the group.”
One tweak to the BoP regulations has caused some controversy with hybrid LMH manufacturers: the speed at which the hybrid (and thus four-wheel drive) can be deployed. Initially, this was set at 120km/h regardless of car; however, to help achieve parity with the two-wheel-drive-only LMDh cars, it has become a variable. Though BoP is normally balanced with weight, in wet conditions four-wheel-drive machinery will invariably have an advantage, hence the pressure to remove said benefit. In the case of Toyota, deployment is restricted to over 190km/h; for Peugeot, 150km/h at its debut race.
This rule appears to remove any advantage of carrying a hybrid, though Jansonnie was philosophical about the situation: “Raising the ERS deployment speed was theoretically the easiest way to balance this, but I would say it is not our favorite option. There was a huge discussion, as you can imagine.” As to whether there remained any benefit to having a hybrid: “It’s a difficult question. Motor racing these days, for manufacturers at least, is electrification, it is hybridization. That is the story we want to tell. For performance, it will be up to the governing bodies to decide but, if you set the deployment speed very high, it becomes electrical ballast.”
There can be no denying that of all the Le Mans Hypercar constructors, Peugeot was the one that nailed the brief when it came to the aesthetics of its 9X8, not least with its bold decision to forego a rear wing. As detailed here, Peugeot felt it could hit the aerodynamic targets set by the BoP (balance of performance) without the need for one.
Sadly, that was not quite the case and through its 18-months of competition the 9X8 has struggled to achieve consistent performance from track to track, hinting at too narrow an adjustment window. At the same time, the BoP calculations have not worked in its favor, particularly when it comes to the team’s choice of using equally sized tires on all four corners. Speaking at the car’s race debut back at Monza in 2022, technical director Oliver Jansonnie noted that the car was designed from the outset to run equally sized tires all around (31/71 x 18), as was specified by the rules for hybrid cars when Peugeot commenced work on the project. The entire concept therefore centered around making these tires work, which he said requires a near 50:50 weight distribution. However, the rules were later changed to allow 29/71 front and 34/71 rear tires, which Toyota took advantage of with its reworked GR010 in 2022. Clearly, the use of a larger rear tire benefits both grip and wear over a stint.
Balance-of-performance woes
For Peugeot, the change came too late. “We would have had to redo everything, and we wondered for some time whether we should accept a delay in the project and start over again,” Jansonnie recalled. In the end, the car maker stuck with the previous tire specification and Jansonnie said it was assured that performance would be balanced regardless of tire size, saying, “We are all in the same boat and we have to make it work.”
Ultimately, the deck did not fall in Peugeot’s favor. Commenting on the revamped 2024 car, Jansonnie said. “We made choices that are no longer the right ones now and this difference in performance was not sufficiently offset by the BoP (balance of performance) in 2023.
“The idea was therefore to go back to a car design that is similar to that of our rivals’ car designs, so that it would then be given equivalent treatment by the BoP. This is why we decided to drop the use of identical 31/31cm tire widths on all the wheels, choosing to fit 29cm tires at the front and 34cm tires at the rear. Strictly speaking, it’s not a new car, as it has the same chassis, but there are a lot of upgrades.”
The change in tire affects the entire philosophy, not least requiring a different aero balance. “For the tires to work effectively, we had to alter the center of gravity of the Peugeot 9X8, which meant moving certain components and working to make others lighter. And in order to have a better aerodynamic balance, we also had to look at redistributing the aerodynamic loads, which resulted in us redesigning approximately 90% of the bodywork components, most notably adding the rear wing. As well as all this, we decided to use this new homologation to add some reliability and performance upgrades to give us the best opportunities in the championship.”
The revised 9X8 made its debut at the Imola round of the WEC in April 2024, however, the team has struggled to understand the new car and in the run-up to Le Mans, performance was notably lacking.
For its return to Le Mans in the prototype classes, Porsche chose to develop a car to the LMDh rule set, rather than building an entirely bespoke Hypercar.
Porsche announced the project on December 16, 2020, revealing its commitment to developing an LMDh prototype for 2023. The decision was primarily influenced by the opportunity to compete in both the FIA World Endurance Championship (WEC) and the North American IMSA WeatherTech SportsCar Championship. Shortly thereafter, Porsche entered a close partnership with Team Penske, giving birth to the new Porsche Penske Motorsport team for international racing. This team operates from two locations: the IMSA headquarters in Mooresville, North Carolina, and the WEC operations in Mannheim, Germany. With the active testing phase of the new prototypes commencing in January 2022, the factory squad is now preparing for its race debut in Daytona.
The 963 made its official race debut at the 24 Hours of Daytona in Florida in January 2023. Prior to this it completed an extensive testing, covering over 33,000km, including the Roar at Daytona.
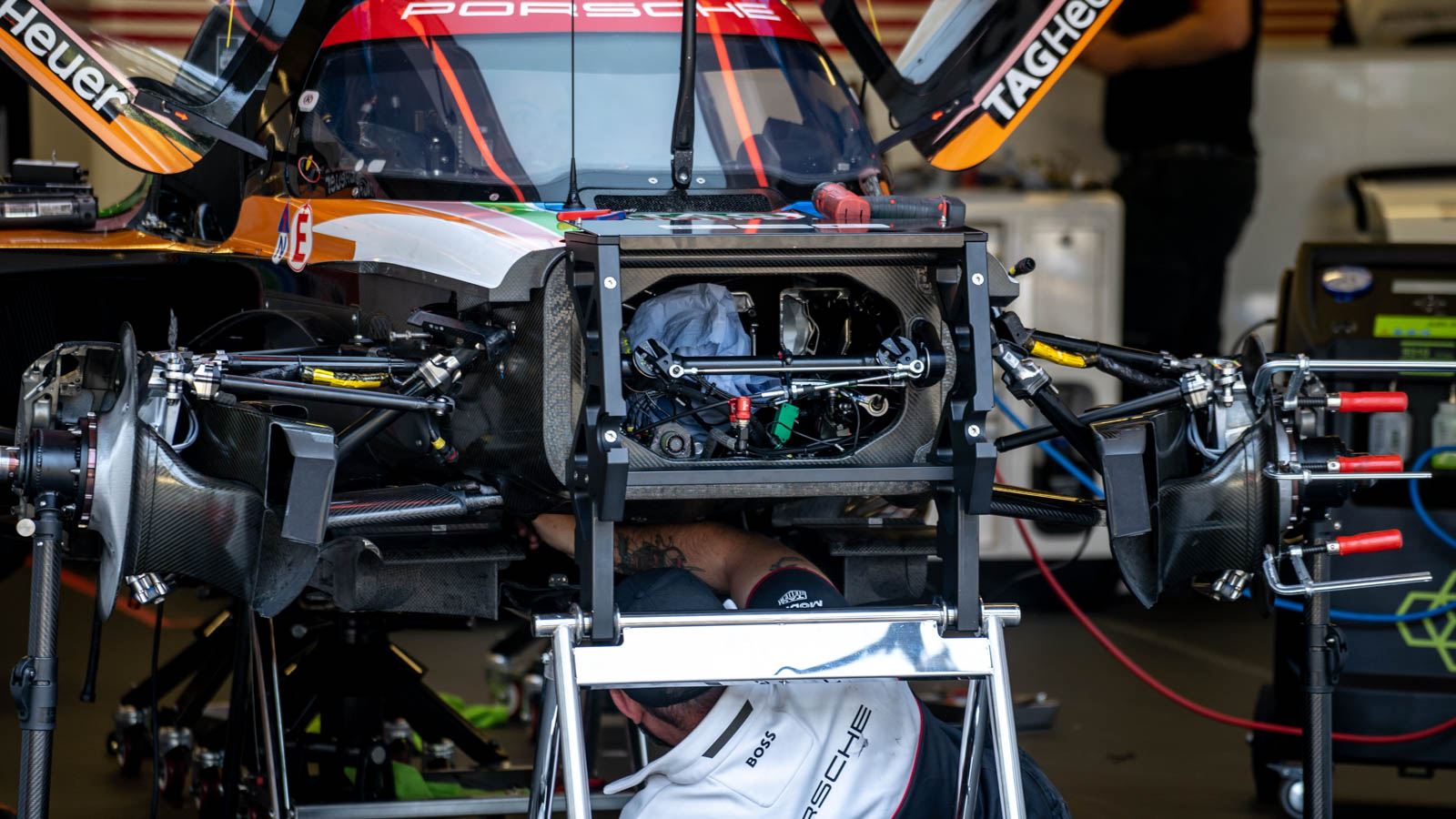
During the Group C era, the legendary Porsche 962 achieved a remarkable feat in 1986 and 1987 by clinching overall victories at Le Mans, Sebring and Daytona in both seasons. Porsche holds a record in all three races, boasting 18 wins at the American endurance classics and 19 overall victories at Le Mans. The team is now hopeful of securing victory number 20 in June 2023, though it faces stiff competition with a still troublesome car.
According to the regulations, all new vehicles in the LMDh category must be based on an LMP2 chassis. Porsche had four potential partners to choose from: Multimatic, Oreca, Dallara and Ligier. After a thorough evaluation process, Porsche made an early decision to collaborate with Multimatic. The Canadian automobile technology company, based in Toronto, is the largest among the four LMP2 manufacturers.
Multimatic also supplies components for other Porsche models such as the Porsche 911 RSR, the Porsche 911 GT3 R, and the Porsche 911 GT3 Cup. As well as the existing business relationship, Multimatic’s extensive production capacities played a crucial role in the decision, especially considering that the Porsche 963 will also be available for customer racing on both sides of the Atlantic in its first year of competition.
The new Porsche 963 features a design that blends modern elements with the brand’s racing heritage. The front section pays homage to the soft shapes of the legendary 956 and 962 models, while the continuous illuminated strip at the rear is a nod to the characteristic hallmark of the current 992-generation nine-eleven model series.
Christian Eifrig, the technical project manager of the Porsche 963, explained, “The regulations give us a performance window. In terms of downforce and lap times, the vehicle must remain within a defined performance range as prescribed by the regulations. This is the only way for the sport’s governing bodies to equalize the cars of different manufacturers using balance of performance. It’s quite challenging to reach this performance window. At the same time, it’s about achieving the typical Porsche look. We had the difficult task of finding the perfect compromise between efficient aerodynamics and an immediately recognisable design language.”
Old-school enginePorsche scanned its back catalog of engines to find a suitable unit for the 936, setling on the 4.6-liter engine last seen in the Porsche 918 Spyder, but which can trace its roots back to the RS Spyder LMP2 car that raced in the first decade of the 2000s.
“The engine features a flat crankshaft and has a very short stroke,” explains Stefan Moser, who headed up the engine development project. “This allowed us to mount it very low, which gives us a low center of gravity and optimum linkage points for the suspension and gearbox. Although the engine was not a supporting element in the 918, its basic rigidity was relatively high – and this also suits us very well.”
The main modification to the engine compared to its road car version was the addition of twin-turbochargers, supplied by Dutch manufacturer Van der Lee. These mildly boost the engine to provide 1.3 bar absolute pressure. The turbos are mounted in a ‘hot’ arrangement in the 90° opening of the vee.
“The good thing is that the engine retains its basic characteristics as a naturally aspirated unit and has a swift throttle response. The relatively low boost pressure builds quickly and therefore there is no so-called turbo lag,” says Moser. According to Porsche, around 80% of the road car parts are retained, though some components required additional reinforcement to allow the engine to work as a structural element in the chassis. The engine is mated to the spec IMSA hybrid system jointly developed by Bosch, WAE and Xtrac, though Porsche appears to have struggled to run the hybrid reliably (unlike Cadillac which appears to have ironed out early teething problems).
“The SC63 is the most advanced racing car ever produced by Lamborghini and it follows our roadmap ‘Direzione Cor Tauri’ laid out by the brand for the electrification of our product range,” stated Stephan Winkelmann, Lamborghini chairman and CEO on its launch in 2023. “The opportunity to compete in some of the biggest endurance races in the world with a hybrid prototype fits with our vision for the future of high-performance mobility, as demonstrated for road legal cars with the launch of the Revuelto. The SC63 LMDh is the step into the highest echelons and into the future of motorsports for our Squadra Corse.”
The SC63 features a bespoke built 3.8-liter twin turbo V8 engine, jointly developed by Lamborghini and Italian engine builder Autotecnica Motori. The decision to use a bespoke engine, rather than a roadcar based unit, stemmed from the fact that so much work would have been needed to adapt any of the company’s roadcar engines, it was easier to start from scratch. The engine is a 90-degree V8, using twin-turbochargers in a cold-vee configuration, chosen in order to keep the packaging simple and reduce CoG height.
Power from the engine and the hybrid system, which is standard across the LMDh-category cars, is limited by regulation to 500kW (680 CV). The Power Unit is managed by a Bosch electronic control unit. The LMDh rule set specifies a standard gearbox, battery and motor generator unit (MGU), which helps to contain the development costs for the prototype.
“Motorsport is, to us, also a valuable and demanding proving ground for our technology,” stated Rouven Mohr, Lamborghini CTO “Our LMDh car, the Lamborghini SC63, is an exciting challenge from both a technical and a human standpoint. The development of our internal combustion engine, aerodynamically efficient bodywork and the overall technical package is a process that has pushed us to constantly raise our own standards. Now, it is time to put the wheels in motion, literally, on track in order to be ready and competitive for the 2024 season. As we develop our LMDh car, we are also mindful of the technology transfer opportunities. We will take our learning experiences from motorsport and apply them where possible to our future production cars.”
Lamborghini chose Ligier as its partner to develop and build the monocoque. As the first manufacturer to select Ligier on an LMDh project, there was freedom for Lamborghini to specify its requirements, including the development of the push rod front suspension design, overall weight distribution and ease of service for critical parts of the car. The bellhousing, which fills the gap between the rear of the engine and the front of the gearbox, positively affects torsional stiffness, and has been designed to house the electric engine.
The bodywork has been designed by Lamborghini’s Centro Stile design department, in conjunction with the race design team. It features very clear brand styling cues throughout the car, including the iconic y-shaped lights at the front and rear.
“From the beginning, my personal briefing to the design-team was that the car needs to be highly functional, but we wanted to create a car that is immediately recognizable as Lamborghini,” said Mitja Borkert, Lamborghini’s head of design at Centro Stile. “The main recognition of the front and rear of the SC63 is driven by the y-shaped signature light. The size of the cabin and the main character of the car is driven by the sporting rules, but we have also implemented our own brand styling cues throughout the car. Integrated into the side panel of the body you can see a NACA duct that was inspired by the air intake of the Countach. When you look at the rear wheel arch, we gave the impression of acceleration towards the front, and this relates to the wheel arch design language of Lamborghini that can also been seen on the Revuelto.”
The cooling layout for the car has decided much of the engineering and design. For example, air intakes into the sidepods behind the cockpit underwent several iterations before a final design was settled upon. The team has incorporated eight different radiators including two intercoolers, one gearbox radiator, one condenser for the air conditioning, one radiator for the Energy Recovery System (ERS), one for the Energy Storage System (ESS) and two water radiators.
One of the limitations of the regulation is that there is only one body kit configuration allowed, and changes that teams are allowed to make to that kit race-to-race are limited. The design team therefore has to take into account the worst-case scenario, such as high ambient temperatures, and manage the thermal efficiency of the car at both IMSA and WEC circuit.
The idea that a rookie team could arrive at the Le Mans 24 Hours with an entirely new car and end up in contention for a place on the podium may seem fanciful. However, that is exactly what Scuderia Cameron Glickenhaus (SCG) did with its SCG 007 Hypercar. The eponymously named outfit is the brainchild of owner James Glickenhaus, a film producer and devout collector of historic endurance racing icons. His and the team’s journey to Le Mans began 15 years ago with construction of the P4/5 by Pininfarina, a one-off, Ferrari Enzo-based road car created through a collaboration with the Italian styling house in 2006, with Ferrari’s blessing. That car morphed into the racing P4/5 Competizione, which competed at the Nürburgring 24h in 2011 and 2012, followed by SCG’s first cars built on a bespoke chassis, the SCG 003 and 004, both of which also raced successfully on the Nordschleife in the SPX class. Glickenhaus has always professed a desire to enter Le Mans and the FIA’s Le Mans Hypercar (LMH) regulations provided him the opportunity to do just that and compete (albeit as an outside bet) for overall honors.
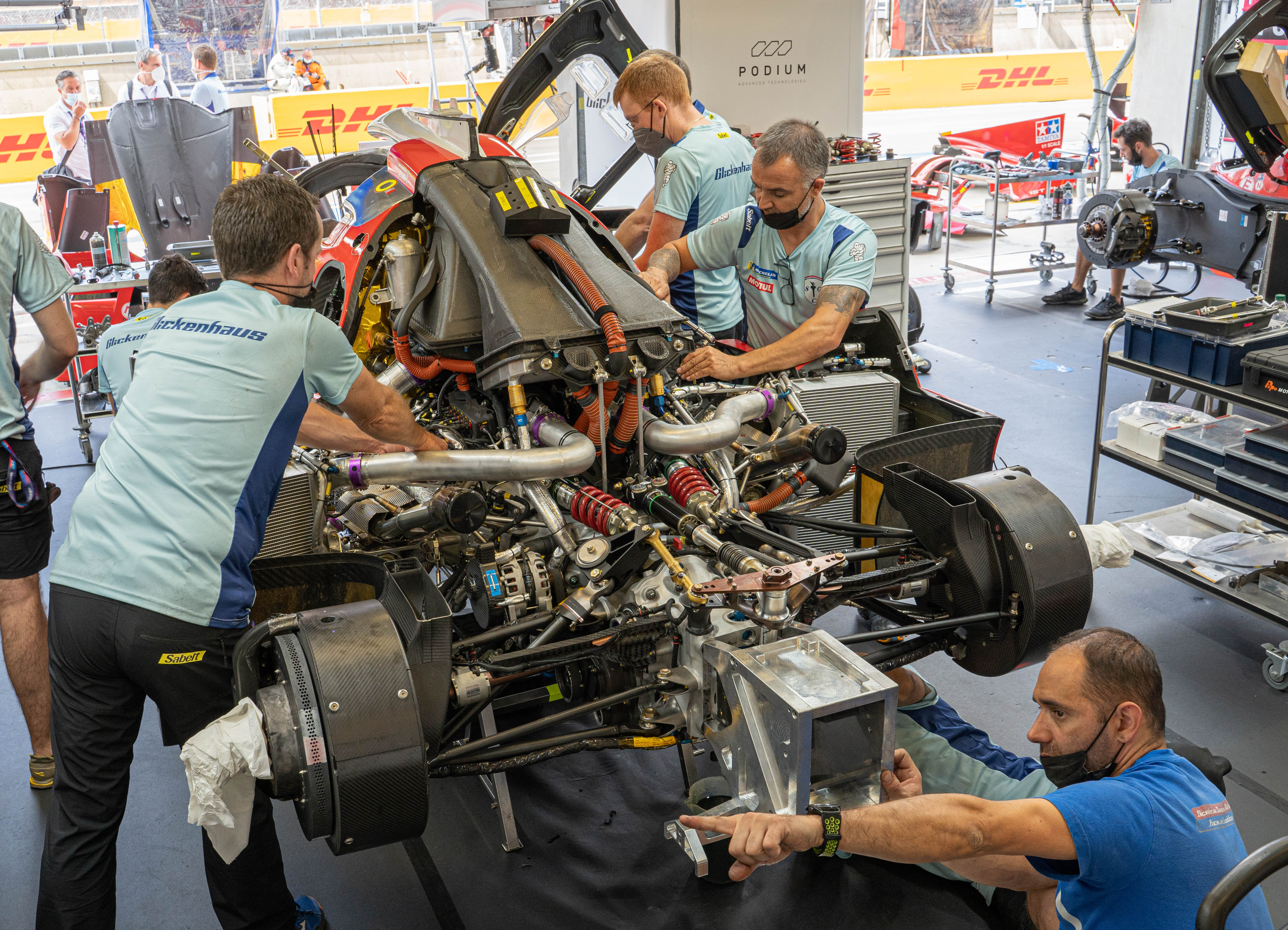
Starting from scratch
Though technically a US team, SCG has a long-standing relationship with Italian outfit Podium Advanced Technologies, which designed and developed both the 003 and 004 GT cars and would also take on responsibility for constructing the 007 Hypercars. In a shrewd move, Glickenhaus and Podium recognized they did not have the expertise to go it alone and signed up a trio of high-caliber development partners for the Le Mans assault. Endurance stalwart Joest Racing, out of contract with Mazda in the IMSA DPi class, provides trackside operations; Sauber Group was contracted to run the aero program; and Pipo Moteurs was tasked with designing a bespoke engine.Despite a highly compressed development schedule and the extensive challenges involved in building an all-new car, SCG made it work. Unlike Toyota, SCG did not have an existing LMP1 as a starting point for its Hypercar design. However, according to Luca Ciancetti, SCG team principal and head of Podium’s motorsport and automotive engineering businesses, the biggest problem was not creating a chassis, but sourcing the powertrain. “When we started, one of the main issues was finding an engine, because in the beginning, the power level was much higher than what we have now,” he says, referencing the first Hypercar rule set released in 2019, which placed peak power at 580kW (784bhp).
“The reality was there was nothing available, which is why we decided to go for a new development with Pipo. That was one of the first decisions we had to make, because it is such a big part of the car,” he recounts. Podium had no existing relationship with the French engine builder, and the latter had never built an endurance race engine. It is better known for its rallying products, which have equipped the likes of Hyundai and M-Sport’s WRC efforts. Regardless, as Ciancetti explains, “They had the I4, which was capable of good performance and reliability, so we decided to do a development program to mirror that [design] along a common crank [to create a V8].”
The resulting 3.5-liter V8 uses the block and cylinder head technology from the rally engines. Given the I4 WRC motors produce approximately 400bhp and cover thousands of kilometers between rebuilds, by doubling up the top end architecture and detuning it (considerably in the end) it had the makings of an ideal endurance engine package. Ciancetti has been impressed with the engine’s seemingly bulletproof reliability and notes that the synergy between Pipo and the SCG/Podium organizations was excellent thanks to both being “two small companies trying to do the best they can while working very hard”.
The team opted to use Xtrac for the transmission supply, which was able to provide an almost off-the-shelf gearbox solution. As with the engine package, says Ciancetti, reliability was the order of the day; however, Xtrac’s standard transverse LMP gearbox still had to be validated for use in Hypercar.
“We had to run some extra structural checks because the cars are very heavy, to make sure the crash loads could be sustained by the transmission,” he says. The transmission is fitted with a shift system supplied by Mega-Line, again selected for its well-proven reliability. As was the case for Toyota, Ciancetti reveals that the lateness of certain rule changes could not be taken advantage of. “Some of the [key] components had already been released when the rules changed, and we did not have time or resources to update everything. Some areas of the car, for example, could be lighter but we are around 1,030kg. We would be happier if we could carry a bit more ballast, but the weight distribution of the car is the one we designed for and it is working quite well.”
Styling exercise
The SCG 007 is undeniably attractive (particularly when compared with the last crop of LMP1 machines) and James Glickenhaus was adamant the car had to measure up aesthetically. Ciancetti recalls, “The initial shape of the car was directly sketched by Jim and that was the starting input for the aero guys. Jim was adamant that he wanted a cool car, and the aero department was definitely very open-minded to keep it as close as possible to what he envisaged.
“Fortunately, though the requirement [regarding aero performance] of the rules is challenging, it is not quite as challenging as it used to be, so we were able to accept some styling guidelines as a starting point. We then had to make up our minds where we wanted to be in terms of other areas of the rules; for example, the size and volume of the crash structures.”
On this last point, both the front and rear crash structures were built to the maximum dimensions permitted by the regulations, ostensibly so that when it came to crash testing sufficient margin of error remained to account for any shortcomings in the team’s finite element analysis (FEA) calculations. This and other aspects of the overall design philosophy were, says Ciancetti, all intended to reduce problems once parts were released for manufacture. “We tried to figure out a comprehensive pre-concept for the car and reduce the risk on the final product,” he explains.
The freedom afforded by the balance of performance-based (BoP) Hypercar rules also forced Podium to revise its approach to the design process. Ciancetti says, “It is definitely a different philosophy because you are generally used to geometry constraints in the rules. Because this is a regulation set based on performance, you must move your mind to work with the huge design freedom you have in terms of shapes and materials, while keeping in mind that whatever you do must match the maximum performance allowed.”
Illustrating the scope of this creative freedom, one of the striking elements of the 007’s bodywork is the rear wing, replete as it is with a series of strakes along its upper surface. The Hypercar rules removed the specific requirement for a dorsal ‘fin’ as seen on previous LMP1 machinery. Instead they only demand a set level of lateral stability be achieved, opening the potential for a more imaginative approach. Ciancetti remarks, “In order to [hit the targets] properly we had to add some vertical fins and looked at a number of different solutions; this one worked very well and Jim liked it a lot.”
Competition reality
No matter how much faith the team placed in the BoP process, Ciancetti is pragmatic about the fact that SCG was competing against the firepower of established manufacturer Toyota, and a well-proven car in the shape of the grandfathered Alpine LMP1.
“If you want to properly manage a program like this, you cannot imagine that because the performance is balanced, it is the same for all teams and budgets,” he muses. “You have to manage your budget in the best way you can, to achieve the best results.”
This, he points out, means that areas not governed by the BoP constraints must be executed to perfection. For example, “Reliability becomes even more important. You can get some help from the rules from a performance point of view, but you will never get any from a reliability perspective. You need a car that is at the right performance level, reliable, simple, easy to swap parts on if you have an issue during the race.”On the subject of serviceability, the Italian says design targets were built in from the start of the project, but it soon became apparent that other areas of the car needed attention once it made its competition debut. For example, based on the car’s running pre-Le Mans, the team expected to experience issues with brake wear. As such, the brake cooling arrangement and caliper/disc change drills were honed. Ciancetti states, “Areas like brake cooling are quite hard to simulate properly, so we had to make some revisions. We got the changes down to 1 min 30.”
However, come the main event, neither SCG 007s suffered any brake woes. There was also some doubt coming into the Le Mans race as to whether the team would be able to triple stint its Michelin tires. “We worked a lot in the time between the [Le Mans] test and now to understand the tire and there is quite a difference in performance as we move between [ambient] conditions,” Ciancetti says. “We have found that we are quite strong when the window is well defined; if it is very cold or very hot, we have a good setup. The middle of the window is a bit trickier for us, it is harder to manage the transition.” Fortunately for SCG, it was able to get on top of wear issues it had experienced earlier in the WEC season, particularly on the rears, which Ciancetti suggests was more due to “the way we were using the car rather than the product”.
Ultimately, SCG achieved what many thought would be impossible: excluding a first lap clash between the #708 and the #8 Toyota, both cars ran almost faultless races at Le Mans, albeit with the #709 never able to match the pace of its sister car. The former was even in contention for a podium place but in the end couldn’t quite match Alpine. James Glickenhaus was upbeat about the car’s performance; however, he cautioned that even for a privateer of substantial means, his continued participation in the WEC is far from assured and hinges on both customer car sales and bringing more sponsors on board. With the arrival of a swathe of new manufacturers in Hypercar from 2022, Glickenhaus’s best opportunity for a podium at the French classic may have passed, but hopefully conditions will prove favorable for the class’s only privateer to remain.[/toggle]
The Vanwall Vandervell team is the latest iteration of what over the years has been known as Lotus and ByKolles Racing, all under the patronage of Colin Kolles. The team’s last car, the CLM P1/01 competed in various guises from 2014 to 2020, gaining something of a reputation for being uncompetitive and somewhat flammable. When the Hypercar regulations were first announced in 2018, the team’s decision to field an entry seemed improbable but it followed through, with the resulting car, the Vanwall Vandervell 680, entering the 2023 WEC.Asked why it chose to go the Hypercar route, rather than LMDh, Boris Bermes, head of operations at the team, explains, “We immediately committed to build a hypercar, because we wanted to build our own car, and we wanted to be present in a top category.” In fact, his engineering team was invested in the concept from the outset. “I remember we did some of the first studies, which we exchanged with FIA on how a Hypercar could be, so we were really spot on from the beginning.”
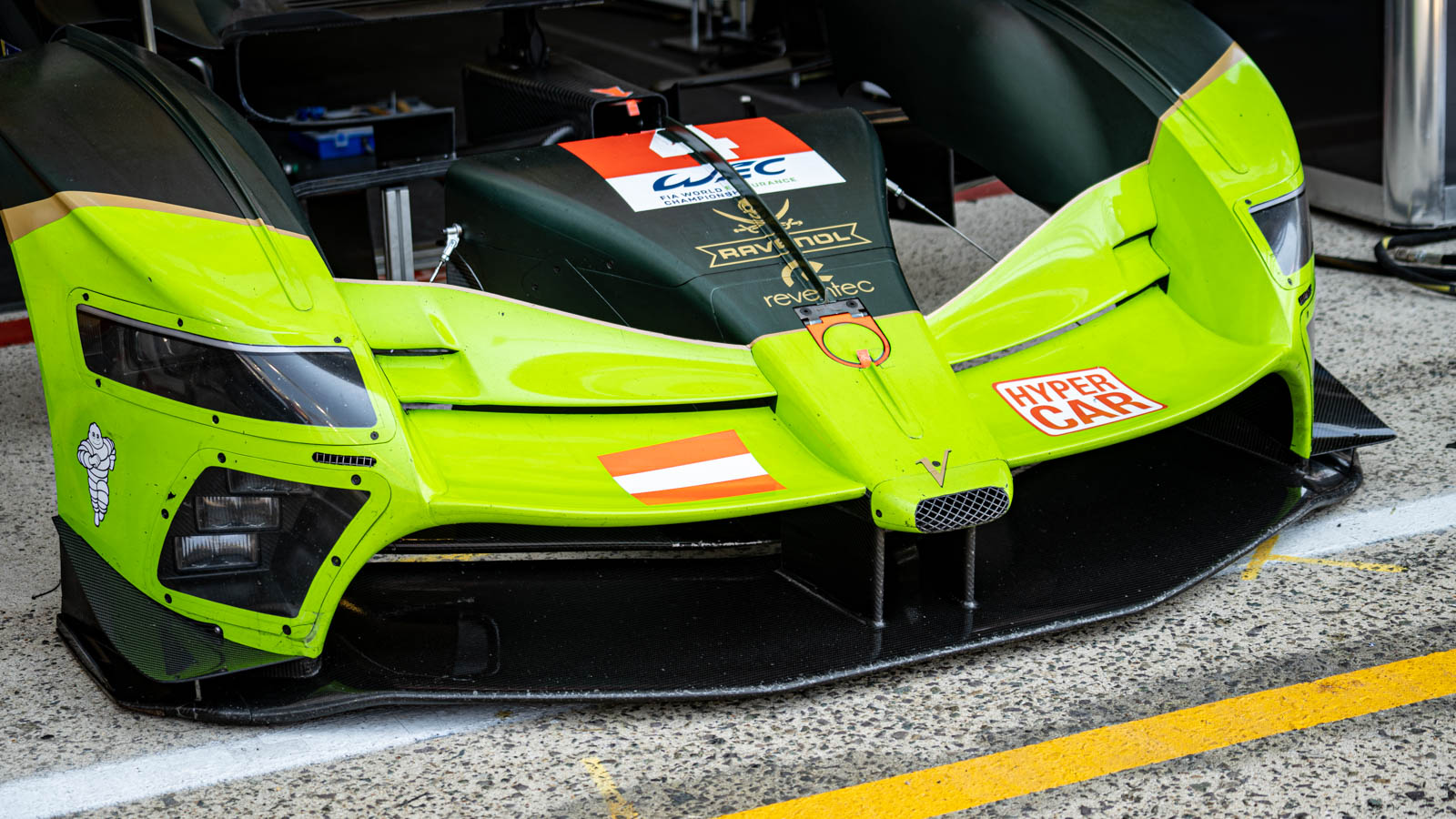
The car is relatively conventional for a modern sports prototype. Based around a composite tub designed in-house (but built by an external contractor), it features torsion bar springing front and rear. Bermes notes that the tub is designed to accept a hybrid system if required (one of the original Hypercar rules iterations stipulated hybrids must be fitted), which would be on the front axle with the battery packaged under the fuel cell.
As to why torsion bars rather than coil springs are used, Bermes says that both packaging and a desire to incorporate the latest technology drove this decision: “We didn’t want to build a car with technologies which do the job but are old stuff. If you build a Hypercar you have to go into the for the latest technologies.”
The aerodynamic development was completed almost exclusively in CFD and, though a road car version is under development, there were no constraints related to brand ID. “We wanted really to have a Hypercar with styling, with modern technologies, which looks different to a P1 car,” says Bermes.
Bermes points out that though the aerodynamic targets are not stratospheric, building a car that hits the upper bound in terms of performance, without exceeding it, while leaving enough scope to vary setup from track to track, is challenging: “They are achievable, but it’s not easy, because the window is too small. I would say in terms of performance it is achievable for everyone. But to be able to make the range of adjustment within this window is a bit tricky. Because it’s a small window, there is not a limit in overall performance its adjustment within that window, you have to get the combination right.”
Proven powertrain
Vanwall opted to stick with the proven package of a Gibson GL458, 4.5-liter, naturally aspirated V8 for use in the 680. Bermes says, “In the last races of LMP1, we put in the Gibson engine because we wanted to have a reliable engine after the disasters with Nissan and AER, which were a nightmare.” However, as the Hypercar rules evolved, this plan was foiled by an increase in permitted power to 585kW, forcing Vanwall to look for other options. Fortunately, this rule later changed back again, to the current 500kW, making the Gibson viable once more. This engine is mated to a 7-speed Xtrac gearbox, which uses a variety of off-the-shelf parts but with modification to suit the 680’s packaging.
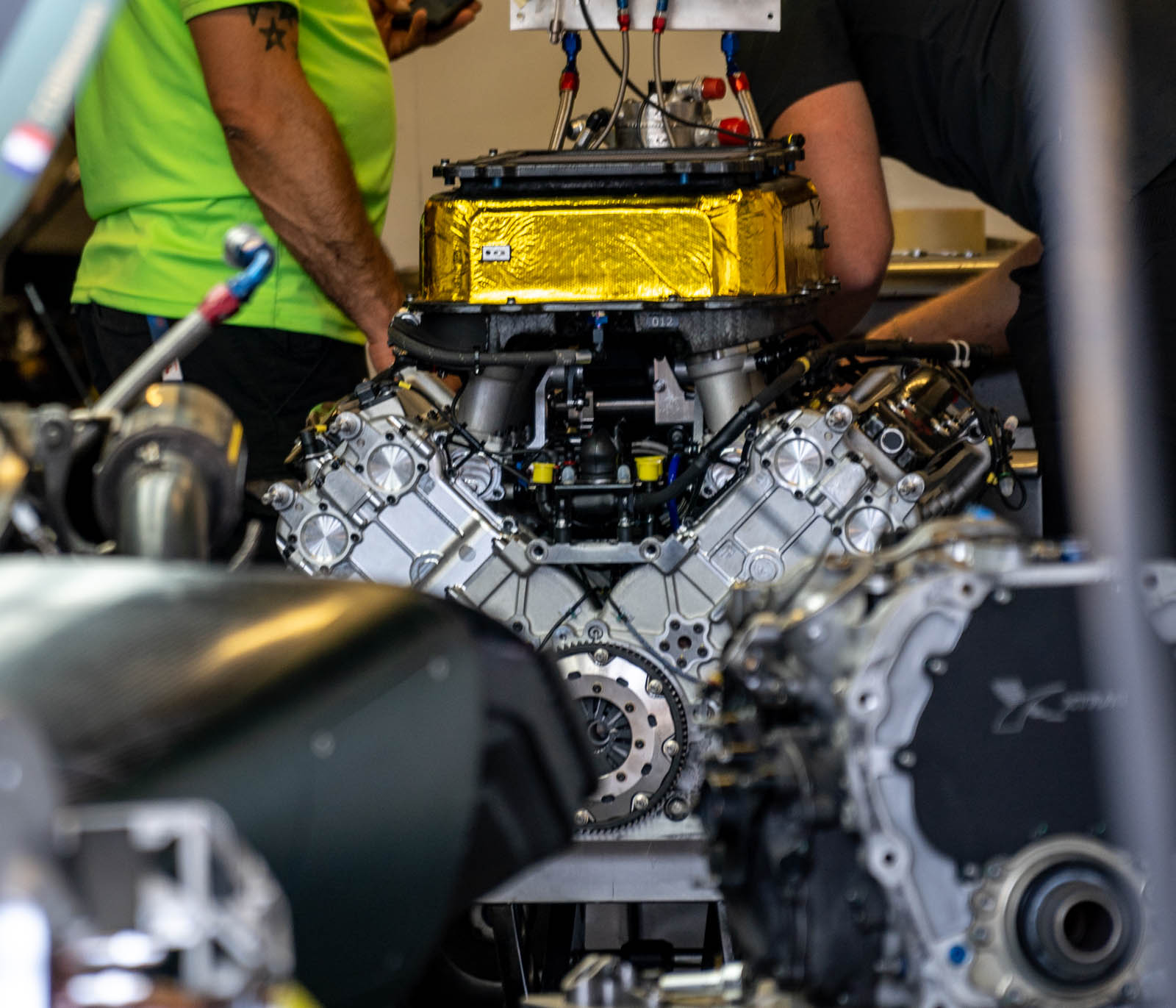
Bermes notes that the team has steadily brought more and more work in house, including much of the composite work (with the exception of the floor and engine cover, which require large autoclaves) and also the entire wiring harness production. It is notable that, looking at the car up close, while far from groundbreaking, the level of fit and finish of the composites and other components appear of a much higher standard than the old LMP1.
[/toggle]
Regulations
The Hypercar class, introduced from the 2021 season, allows two types of cars: LMH (Le Mans Hypercar) and IMSA’s LMDh (Le Mans Daytona Hybrid). The former can have four-wheel drive if a hybrid powertrain is used, LMDh cars meanwhile are rear-drive only, and fitted with a spec hybrid system.
Evolution of the hypercar rules
Having announced that a new class would be developed to replace LMP1 at the 2018 Le Mans 24 Hours, the FIA released the first of many iterations of the technical regulations in December that year, specifying that production-based powertrains were required. They also established that manufacturers had to produce a minimum of 25 road cars equipped with the race car’s combustion engine and energy recovery system (ERS) by the end of their first season, increasing to 100 cars by the end of the second season.
As a result, non-OEM race car constructors such as Oreca and Dallara were effectively eliminated from building Hypercars. The regulations did not include a previously proposed off-the-shelf hybrid solution. The power output limit for the combustion and electric hybrid system was set at approximately 950hp (710kW), which was lower than the initial figure announced in June. The maximum output for the combustion engine was adjusted to 508kW (681hp) instead of 520kW (700 hp), while the electric unit’s power output remained unchanged at 200kW. Additionally, diesel power was banned, and a cost cap of €3m (US$3.4m) was imposed on the supply of ERS systems from manufacturers to customer teams. The FIA also stated that an ERS manufacturer could not supply systems to more than three competitors without formal approval.
The minimum weight of the new-generation cars was increased from the initially specified 980kg (2,160 lb) to 1,040kg (2,290 lb), and the maximum length was set at 5,000mm (200 in). The maximum cockpit width was also expanded to 2,000mm (79 in).
In March 2019, the FIA added to the rules to allow manufacturers to enter race cars based on roadgoing hypercars. This change was prompted by manufacturers expressing interest in aligning their production and race activities more closely due to budgetary and platform availability concerns. Road car-based hybrid systems would have had fewer regulation constraints than bespoke race versions. This also coincided with target lap time for the new cars being increased from 3:20 to 3:30, while movable aerodynamic devices that the original regs included were removed due to cost considerations.
The rules would go through various further iterations before the first cars hit the track in 2021, with notable changes – such as the removal of weight limits on engines and transmissions – making life difficult for early adopters like Toyota. The various stipulations regarding roadgoing cars and production-based engines also fell by the wayside. The final rules would see power output limited to 500kW, and a minimum weight of 1,030kg (down from 1,100kg).
The full WEC Le Mans Hypercar regulations can be downloaded here
The FIA regulations for LMDh can be downloaded here
Key to the Hypercar class at Le Mans is the implementation of balance of performance (BoP) rules which artificially restrict the performance of cars. This covers both powertrain and aero performance (the former monitored via the use of torque sensors on all drive axles).
The first stage of the BoP is achieved at the homolgation stage. The regulations set an aerodynamic efficiency target of around 1:4 L/D, although this was upped slightly in a late revision to the rules. To assess each Hypercar design, they are run at Sauber’s wind tunnel in Switzerland across a wide range of ride heights, airspeeds and yaw angles to create a comprehensive aero map. Once a car is passed, the FIA conducts a 3D scan of the bodywork to create a reference set of CAD data. At any point in the season, the FIA can seize a car and rescan it to check it remains in compliance with its original homologation.
The second step is “platform equivalence”. Two different technical rulebooks govern the Hypercar class: Le Mans Daytona h (LMDh) regulations based on the use of common parts, and Le Mans Hypercar (LMH) regulations which offer manufacturers greater freedom. The two sets of regulations are very similar, but their different conception may call for performance adjustments. To achieve this, “platform equivalence” is applied across all cars of the same type, taking on board the performance levels of the best LMDh-type car and the best LMH-type car.
The final step – “manufacturer compensation” – considers the individual performance of each manufacturer based on the in-race data collected. We must emphasise that “manufacturer compensations” – whatever their nature – are used sparingly and only where the data is deemed to be sufficiently robust, which takes several races. However, for Le Mans, the BoP is not based on performance during the previous WEC races of the season, only on the last year’s 24Hrs, with simualtion used to extrapolate these performances.
A notable new addition to the BoP rules for 2024 is a two stage, speed linked llimit on power output, intended to help balance top speeds across the field. The result being that competitors are either given an extra power allowance over 250kph, or have permitted power cut.